A powder coating booth is the heart of any finishing operation, ensuring consistent quality, efficient material usage, and a safe working environment. However, neglecting its maintenance can lead to costly downtime, uneven coatings, and premature equipment failure.
Regular upkeep of your powder coating booth isn’t just about cleanliness—it’s a proactive strategy to maximize productivity and protect your investment. From clearing accumulated powder in cyclones to monitoring critical components like sieve screens and pressure differential gauges, small daily and weekly actions can prevent major disruptions.
In this guide, we’ll break down essential maintenance steps to keep your powder coating booth running at peak performance, reduce waste, and deliver flawless finishes every time. Let’s dive into the key practices that industry experts swear by.
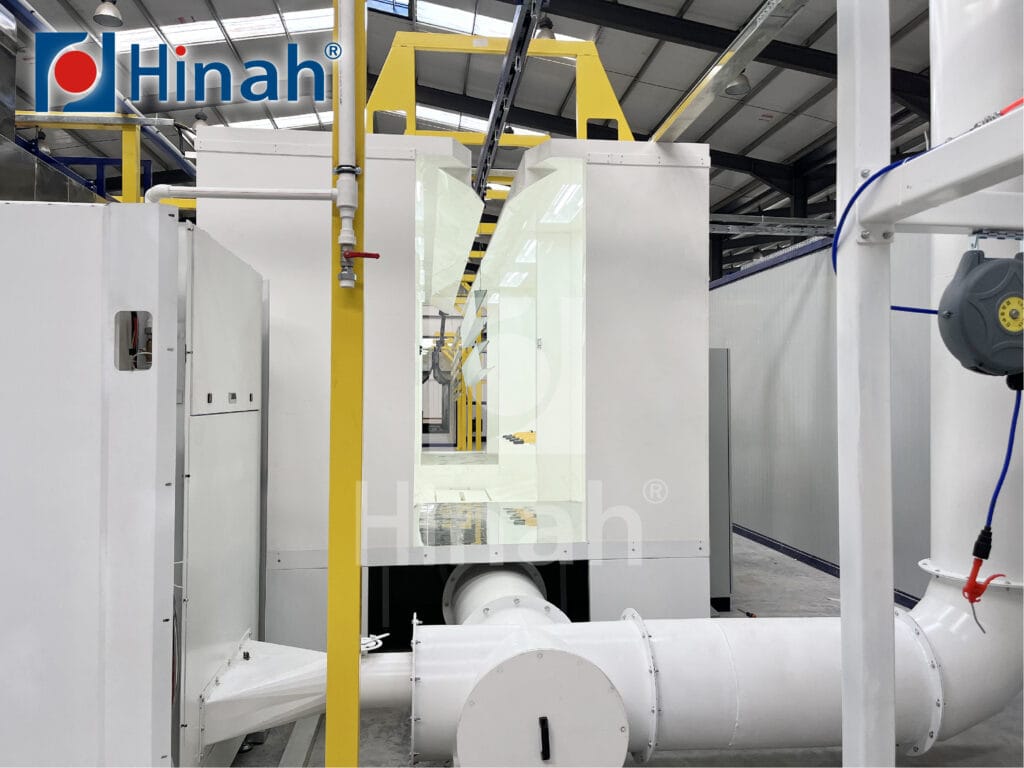
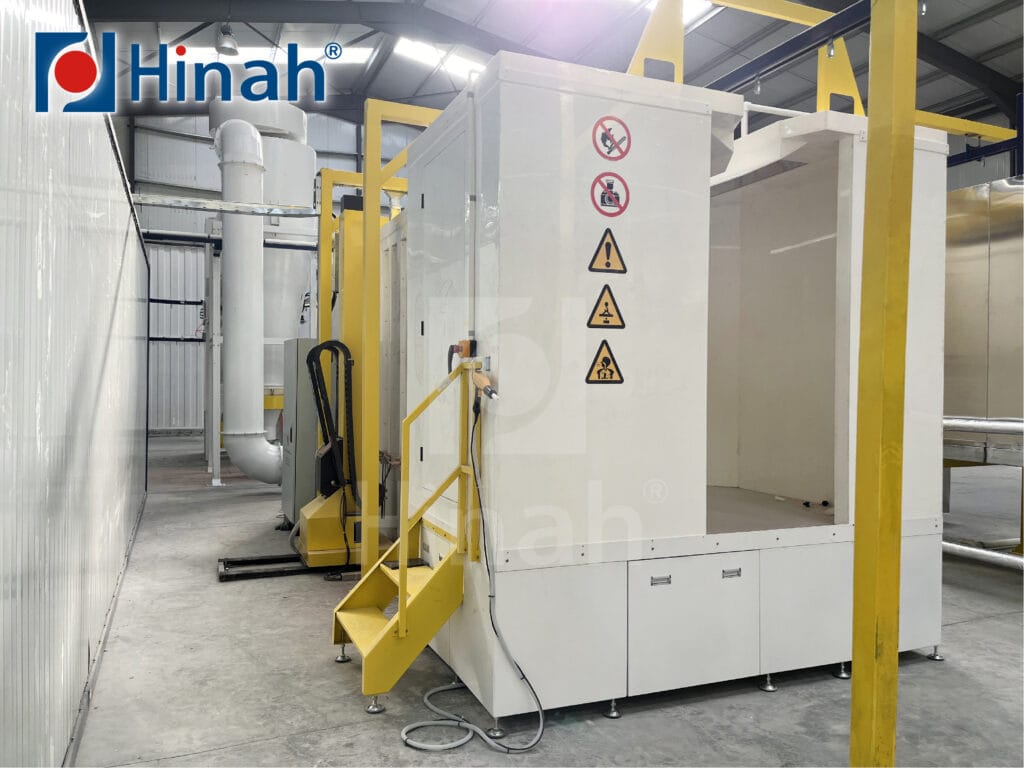
I. Daily Maintenance for Your Powder Coating Booth
- Clean Accumulated Powder Deposits
Daily removal of excess powder is critical to maintain airflow and prevent contamination. Start by emptying the large cyclone separator to avoid blockages that hinder powder recovery efficiency. Next, clear residual powder from the recovery barrel, ensuring no overflow occurs between batches. Finally, thoroughly wipe down the booth’s interior, focusing on walls, floors, and grates, as accumulated powder can clog filters or even pose a fire hazard if left unaddressed.
- Inspect Sieve/Screen Functionality
The sieve’s performance directly impacts coating quality. Begin by testing the screen’s lifting mechanism to ensure it operates smoothly without jamming—apply lubricant to hinges or rails if movement feels stiff. Simultaneously, inspect the sieve’s sealing around its edges; gaps or misalignments can allow oversized particles to bypass filtration, leading to uneven spray patterns and defective finishes.
- Monitor the Pressure Differential Gauge
This gauge acts as your booth’s “health monitor.” Maintain a pressure range of 1.0–2.0 KPa for optimal airflow. Readings above 2.0 KPa indicate (severe filter clogging) or a malfunctioning filter-cleaning system. If the pressure exceeds this threshold, immediately clean the filters using compressed air at 4–4.5 bar. Persistent high pressure may necessitate filter replacement to restore performance and prevent costly downtime.
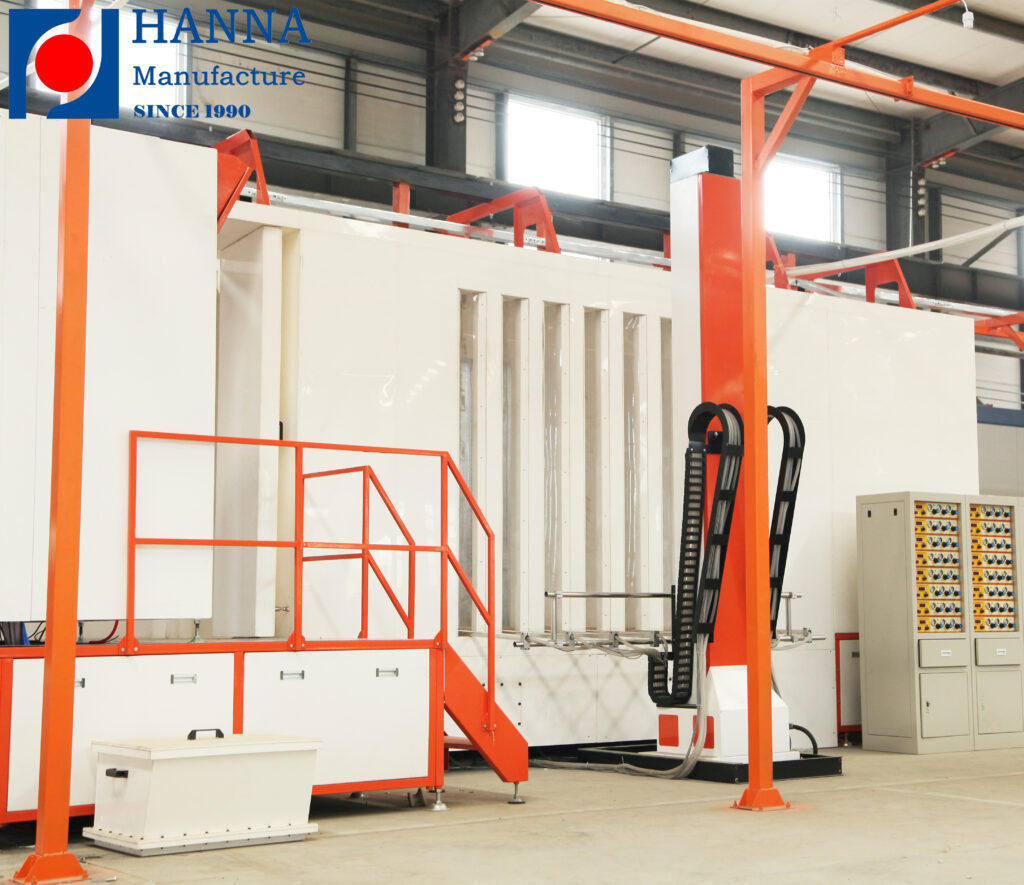
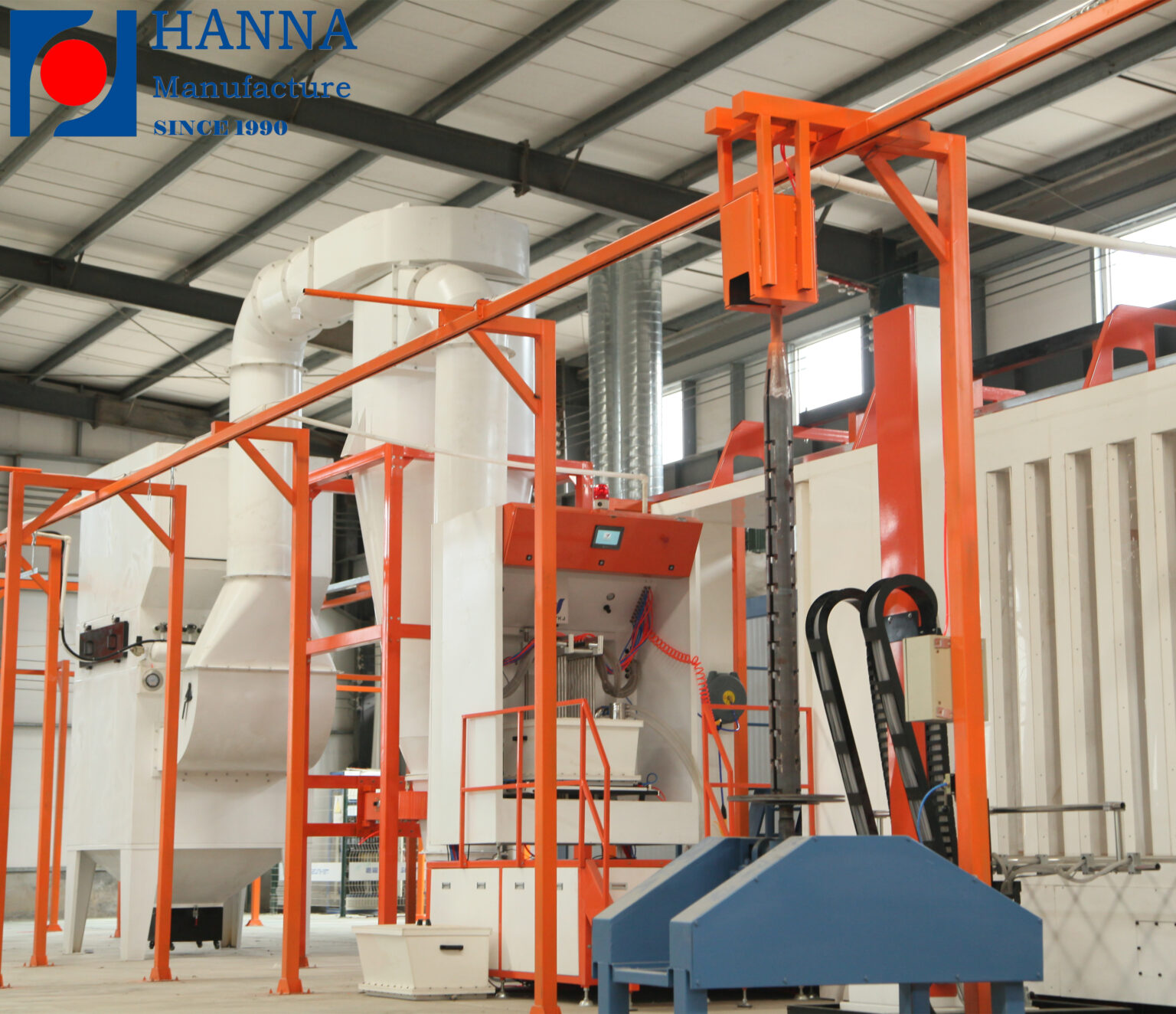
II. Key Components to Monitor in Your Powder Coating Booth
Regular inspections are vital to prevent hidden issues and extend your booth’s lifespan. Focus on these three critical components during routine checks:
Screen/Sieve Inspection & Maintenance
- Check for Damage: Inspect the mesh for tears, warping, or holes. Even minor defects allow oversized particles to pass, causing rough finishes.
- Clean the Mesh: Remove caked powder with a soft brush or low-pressure compressed air (≤3 bar) to prevent clogging.
- Replace When Necessary: Upgrade the mesh if damage exceeds 5% of the mesh area or powder bypasses filtration.
Filter System Health Check
- Monitor Pressure Gauge Trends: Ensure readings stay within 1.0–2.0 KPa. Consistently high values (>2.0 KPa) indicate clogged filters or weak cleaning pulses.
- Test Cleaning Pressure: Verify compressed air pulses reach 4–4.5 bar during automatic cleaning cycles. Low pressure fails to dislodge stubborn powder.
- Inspect Seals & Housing: Replace cracked filter seals to prevent powder leaks, which reduce powder recovery rates.
Airflow & Ventilation Audit
- Check Airflow Balance: Confirm uniform suction across the powder coating booth using an anemometer. Uneven airflow causes overspray buildup.
- Clear Ductwork: Remove powder deposits from exhaust ducts monthly to prevent blockages and fire hazards.
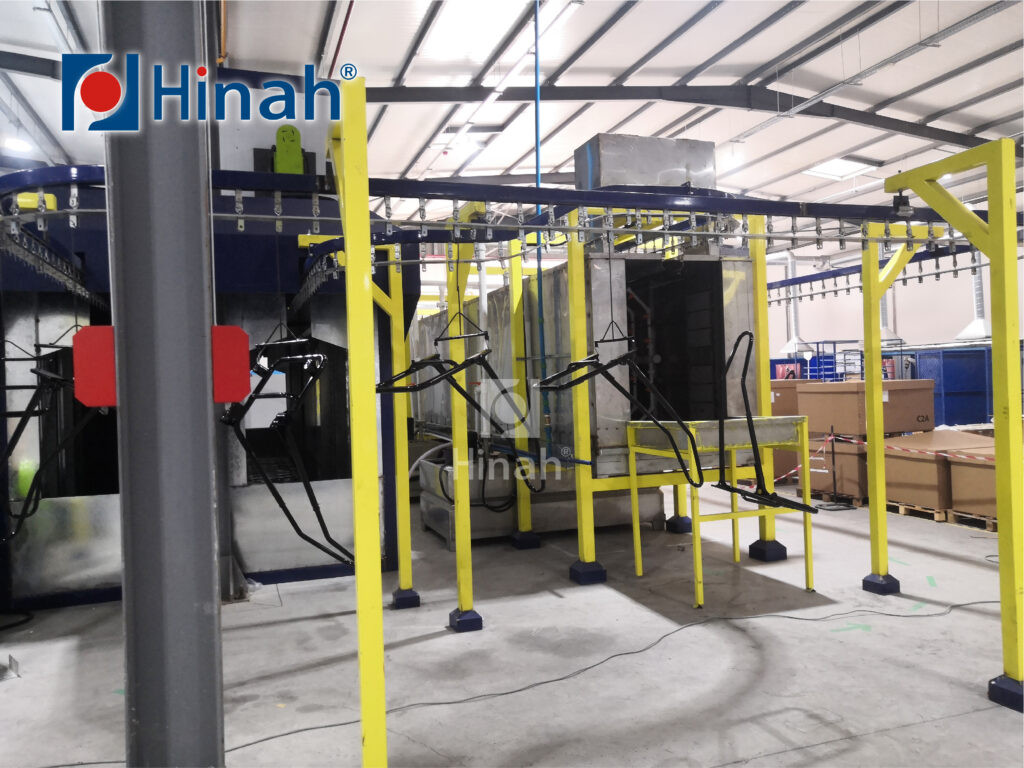
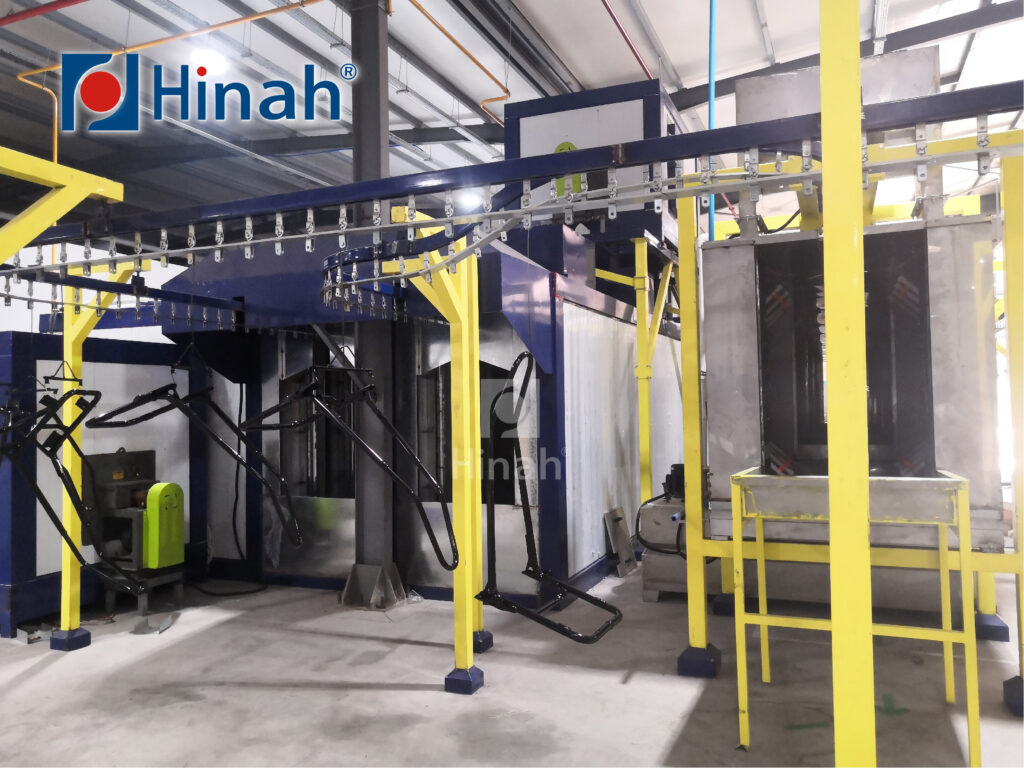
III. Conclusion
Consistent maintenance of your powder coating booth is not just a task—it’s a strategic investment. By adhering to daily cleaning routines, conducting regular inspections of screens and filter systems, and promptly addressing pressure differential gauge anomalies, you significantly reduce unplanned downtime, slash material waste by up to 30%, and ensure flawless coating quality. Over time, these practices lower operational costs and extend equipment lifespan, delivering a rapid return on effort.
Don’t let neglect erode your productivity. Start implementing these steps today, and for a tailored maintenance plan or professional support, [contact our experts] or download our free Powder Coating Booth Maintenance Checklist to stay ahead of issues.