Designing an automatic powder coating line demands precision to maximize efficiency, quality, and sustainability. From hanger layouts to curing processes, every decision—like conveyor systems or robotic spray integration—directly impacts operational costs and finish consistency.
This guide breaks down critical planning steps, including energy-efficient heating, spray booth airflow optimization, and smart workflow design. Whether upgrading or building new, these insights ensure your powder coating line delivers high-performance results while minimizing waste. Let’s explore the essentials.
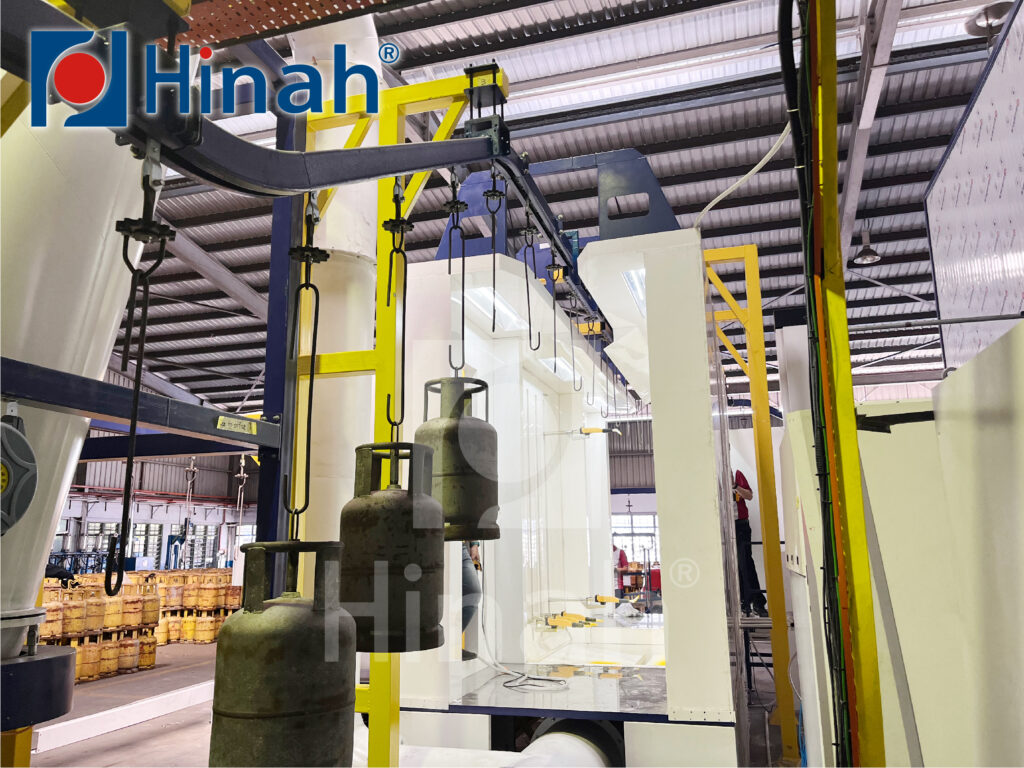
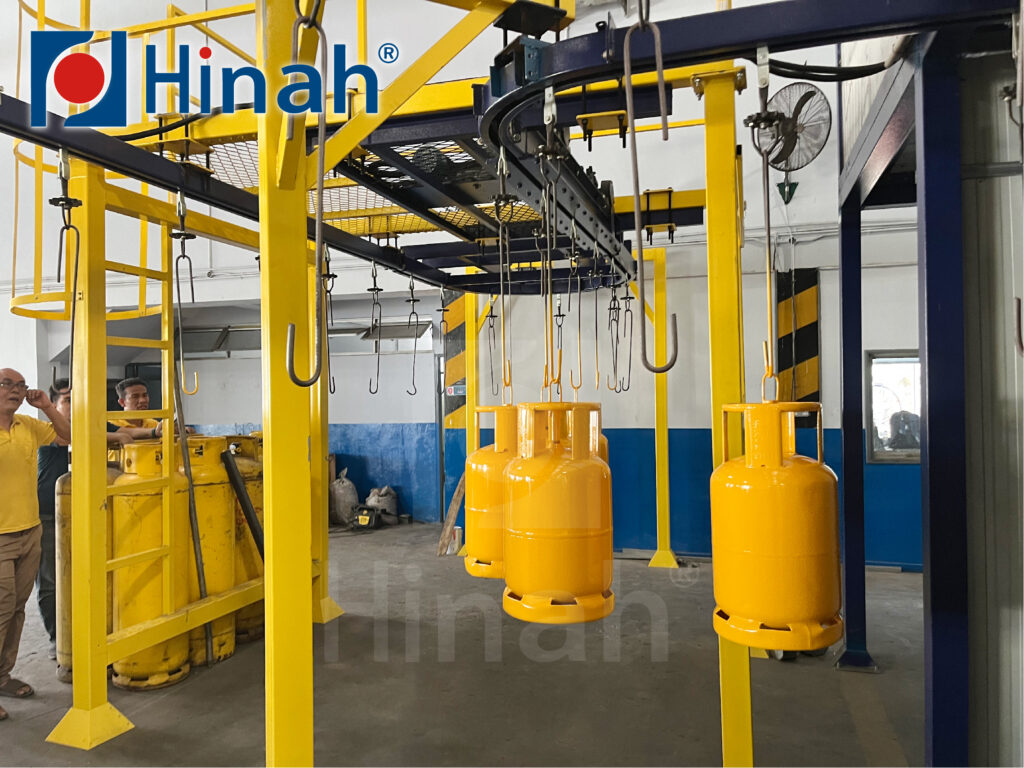
1. Hanger Design for the Automatic Powder Coating Line
Effective hanger design is pivotal to the success of an automatic powder coating line, ensuring seamless operation and uniform finishes. Hangers must prioritize easy installation and removal—features like magnetic locks or modular designs minimize downtime during part loading. Equally critical is uniform distribution: spacing hangers appropriately prevents overcrowding, optimizes airflow, and guarantees consistent powder coverage. Durable, heat-resistant materials (e.g., stainless steel) are essential to withstand repetitive curing cycles, while adaptable shapes accommodate diverse part geometries, reducing rework for complex components.
To maximize efficiency, test hanger layouts in trial runs to identify issues like weight imbalance or airflow disruption. A well-designed hanger system not only enhances productivity in your powder coating line but also reduces defects, maintenance costs, and energy waste.
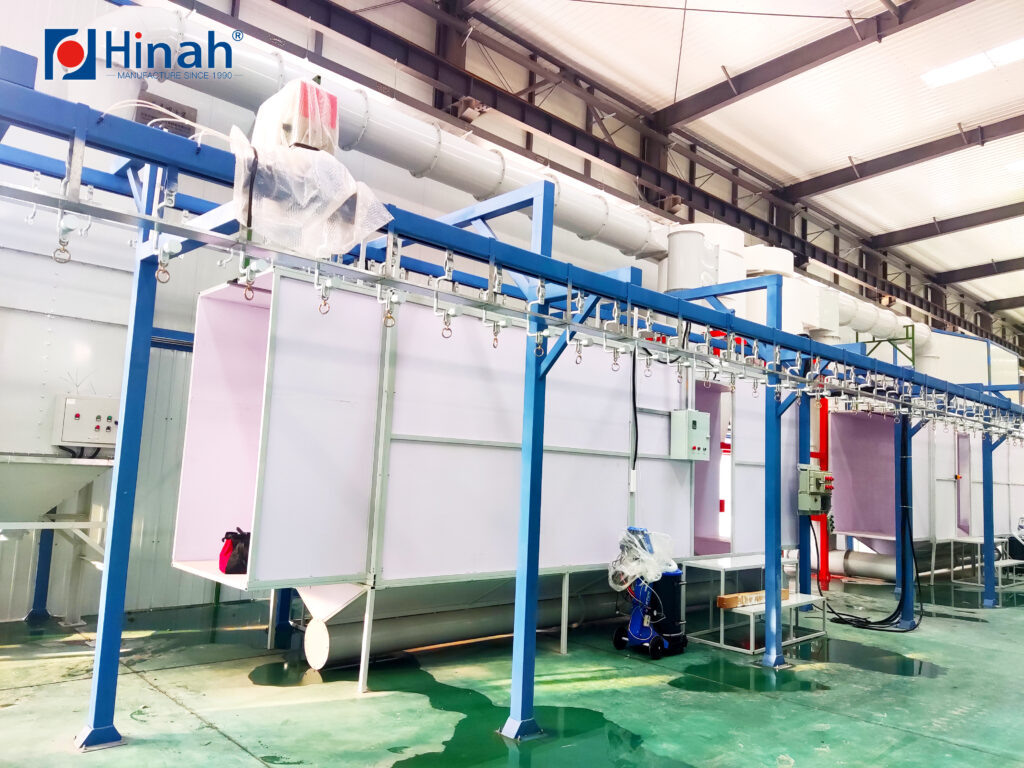
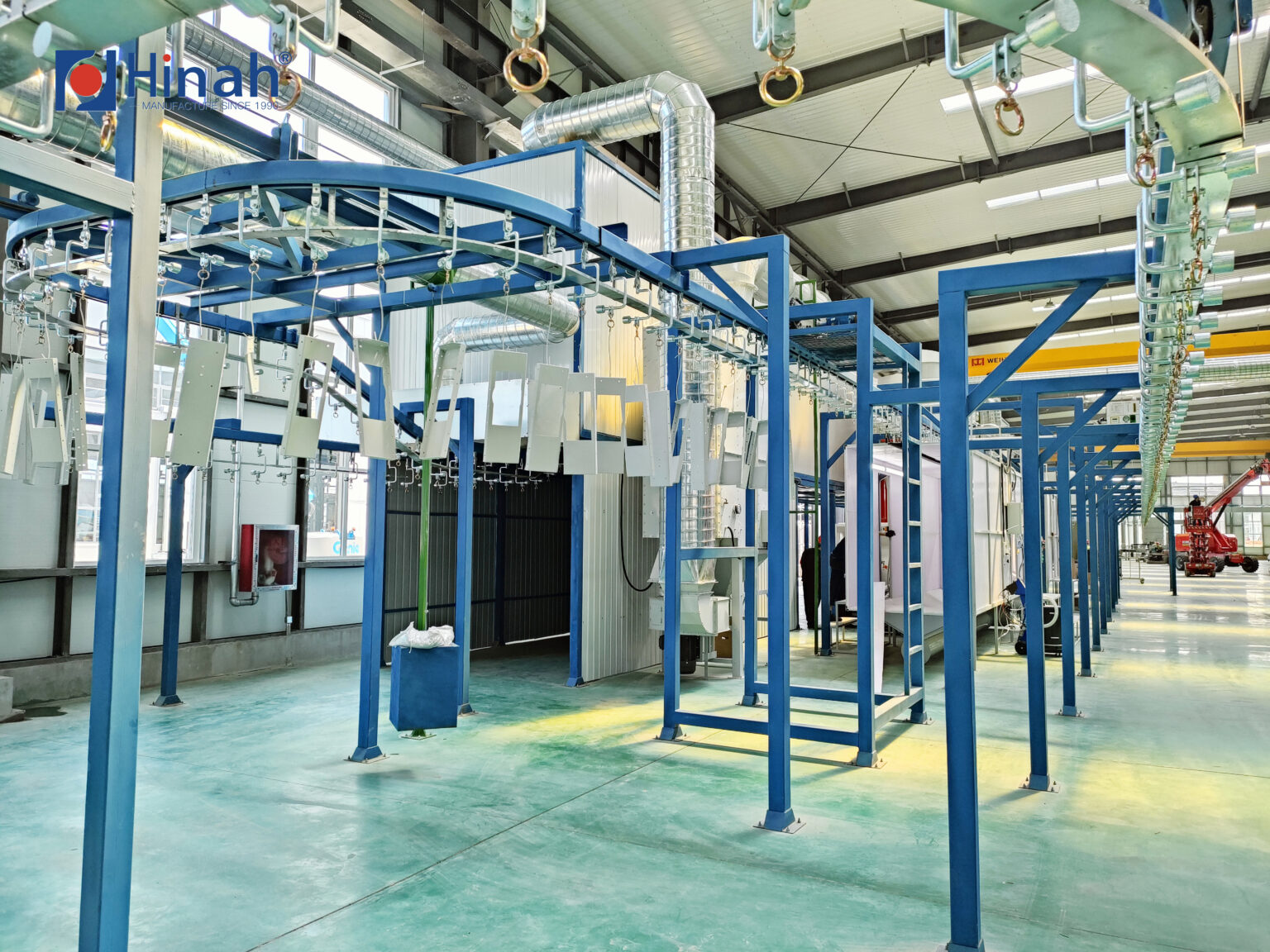
2. Choosing the Right Conveyor System
The conveyor system forms the backbone of an automatic powder coating line, directly impacting throughput and operational efficiency. Overhead (suspended) conveyors excel in high-volume production, offering flexibility for vertical space utilization and heavy parts, while ground conveyors (e.g., floor chains) suit smaller facilities or lighter components. Prioritize systems with low maintenance requirements and scalability to adapt to future production demands. Energy-efficient designs, such as variable-speed drives, further reduce costs while ensuring smooth material flow through coating, curing, and cooling stages.
3. Optimizing Spray Methods
Spray method selection hinges on balancing speed and precision. Single-layer dual-station setups allow simultaneous coating of two parts, ideal for high-throughput lines with simple geometries. Conversely, intermittent rotating dual-side spraying enables 360° coverage in a single workstation, reducing footprint but requiring precise timing controls. Both methods demand alignment with part complexity and line speed—uneven spray patterns or rushed cycles risk defects like orange peel textures. Advanced electrostatic guns or automated reciprocators can enhance uniformity while minimizing overspray.
4. Integrating Robotic Spray Technology in Your Automatic Powder Coating Line
Robotic spray systems elevate consistency and reduce waste in an automatic powder coating line, though cost remains a key consideration. Dedicated powder-coating robots, programmed for specific part geometries, deliver unmatched repeatability for high-mix production, while general-purpose robotic arms offer flexibility at lower upfront costs. Pairing robots with vision systems or AI-driven path optimization ensures precise coverage, even for intricate designs. While initial investments are higher, the long-term payoff—reduced rework, material savings, and faster cycle times—often justifies the upgrade for quality-focused operations.
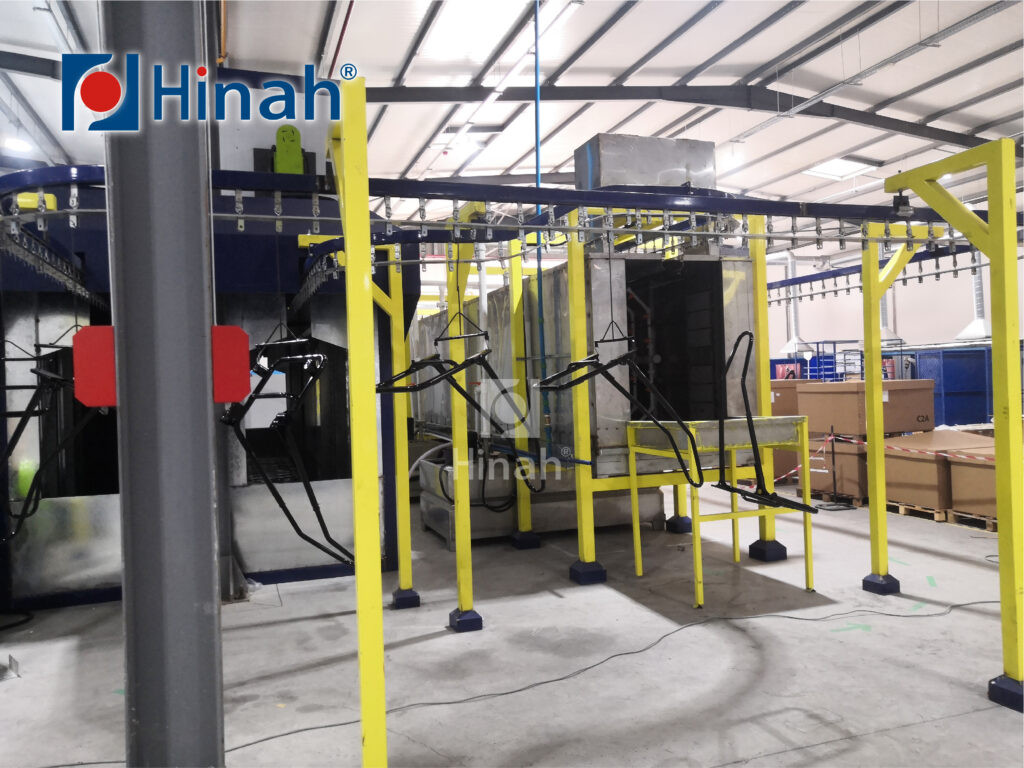
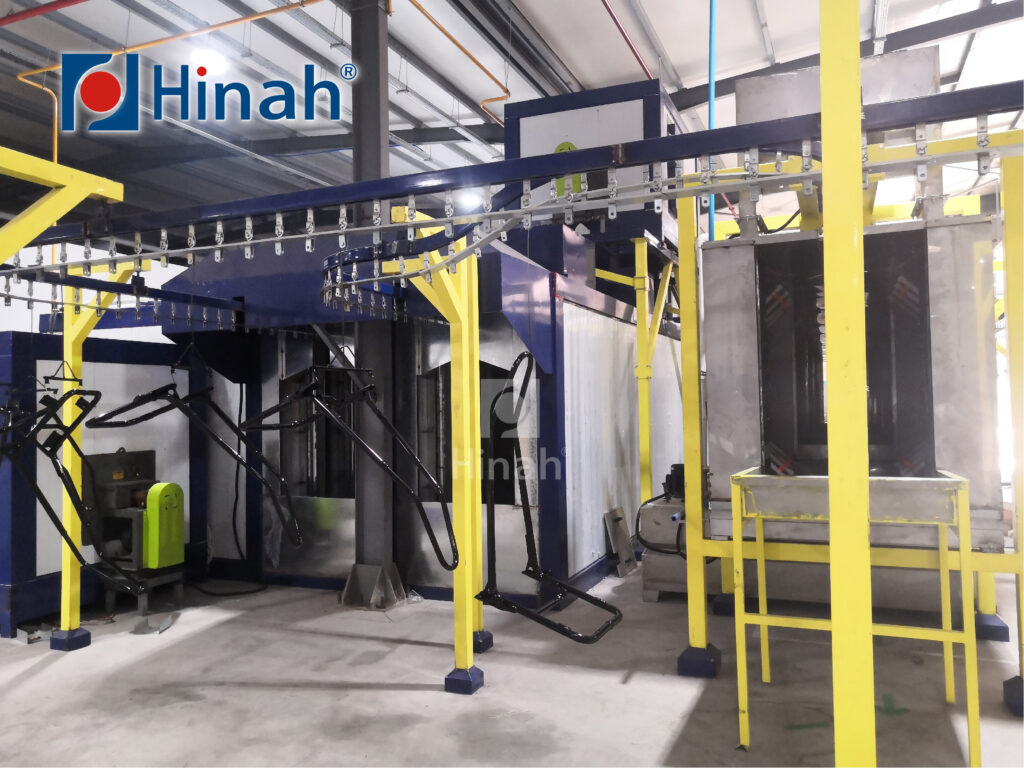
5. Energy-Efficient Curing and Drying Processes
The curing stage in an automatic powder coating line demands careful selection of heating methods to balance energy efficiency and performance. Infrared (IR) systems provide rapid, targeted curing with lower energy consumption, while convection ovens offer uniform heat distribution for complex parts. Optimize oven length and insulation to minimize heat loss, and incorporate heat recovery systems to reuse waste energy. Precise control of temperature and dwell time ensures proper cross-linking of the powder, preventing under- or over-curing defects. Sustainable designs not only reduce operational costs but also align with environmental regulations.
6. Managing Flow and Cure Times in the Powder Coating Process
The flow-coating (leveling) stage is critical for achieving smooth, defect-free finishes in an automatic powder coating line. A sufficiently long flow zone allows the powder to melt and level evenly before curing, while precise temperature control prevents issues like blistering or orange peel. Ensure the curing tunnel’s length matches the line speed to maintain consistent heat exposure. Poorly managed flow or cure times can lead to rework, wasting time and materials. Monitoring tools, such as infrared sensors, help maintain optimal conditions for flawless results.
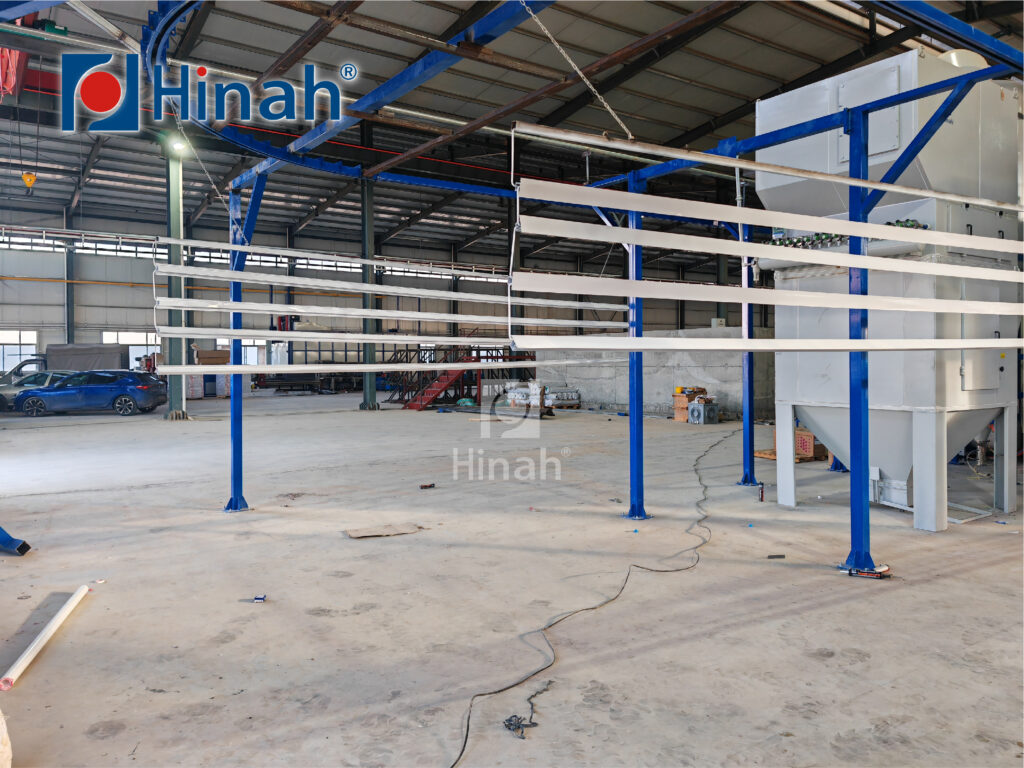
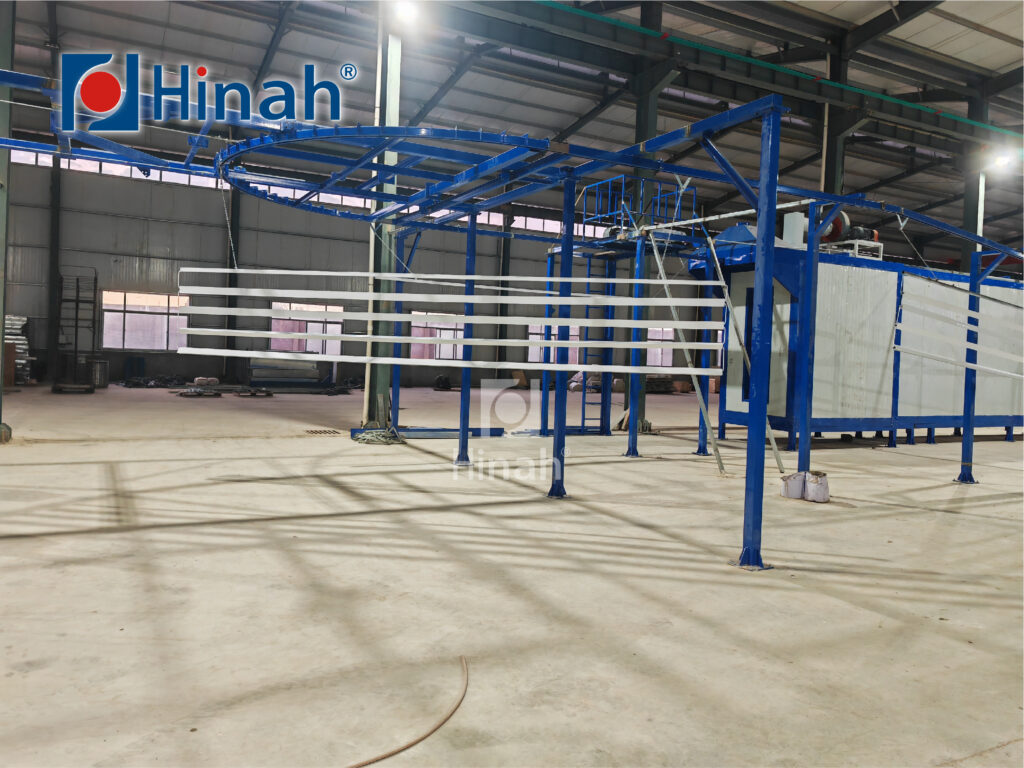
7. Designing the Spray Booth for Your Automatic Powder Coating Line
A well-designed spray booth is vital for maintaining air quality and coating consistency in an automatic powder coating line. High-efficiency air filtration systems (e.g., ISO Class 5/6) capture overspray and contaminants, ensuring a clean environment and reducing defects. Downdraft or crossdraft airflow patterns direct particles away from coated surfaces, while explosion-proof features enhance safety. Regular filter maintenance and booth sizing tailored to part dimensions further optimize performance. This setup not only improves finish quality but also extends equipment lifespan.