In the competitive world of surface finishing, powder coating line operators constantly seek to maximize throughput while minimizing waste. Yet many overlook a critical lever hidden in plain sight: electrostatic voltage. Far more than a technical setting, voltage directly dictates your line’s efficiency, quality, and ultimately – your bottom line.
Why does voltage hold such power? At its core, higher electrostatic charge dramatically improves powder transfer efficiency. This means more material adheres to the target, reducing overspray and reclaim cycles. The result? Faster production speeds, consistent coating quality, and maximized powder coating line output. In this guide, we explore how mastering this parameter unlocks unprecedented productivity gains.
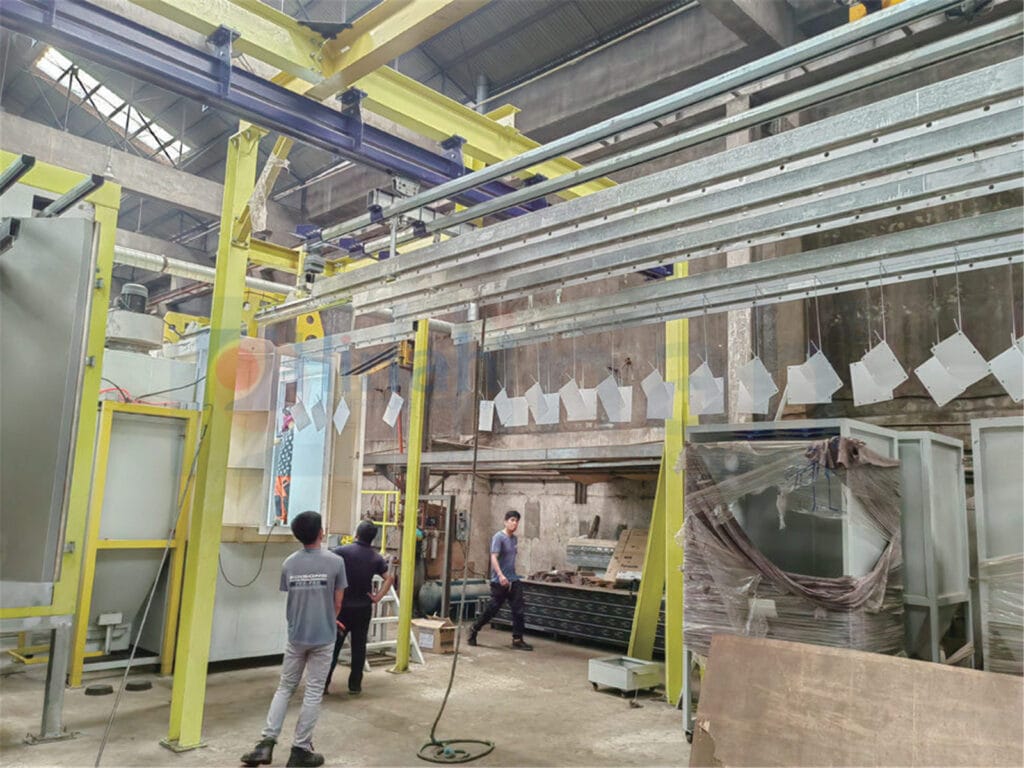
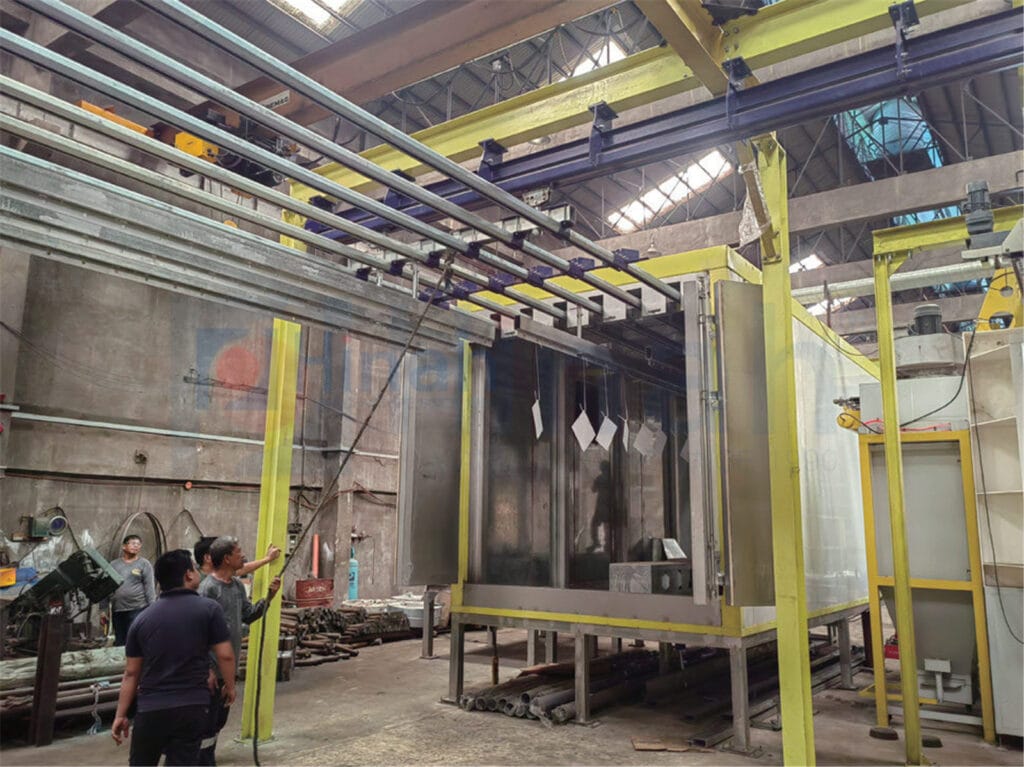
Electrostatic Voltage Basics for Coating Lines
Electrostatic voltage is the engine of efficiency in any modern powder coating line. Operating within the 60–100 kV range, it creates a high-intensity electric field between the spray gun and the grounded target. This critical force charges powder particles, enabling them to overcome aerodynamic resistance and adhere tightly to surfaces. Without sufficient voltage, powder dispersion becomes erratic, compromising line-wide consistency.
Why 80–100 kV is the Industry Sweet Spot
While 60 kV is the functional minimum, most industrial powder coating lines achieve peak performance at 80–100 kV. This optimal range maximizes powder transfer efficiency – the percentage of material that successfully adheres to the target. Higher voltage (within this band) strengthens the electrostatic attraction, directly translating to:
- Reduced waste (less overspray and reclaim cycles),
- Faster coverage (accelerated production speeds),
- Uniform film thickness (minimizing rework needs).
Operating below 60 kV risks poor adhesion and uneven coatings, forcing costly line slowdowns. Conversely, exceeding 100 kV may cause back-ionization (surface defects). Thus, precision voltage control isn’t optional – it’s foundational to powder coating line throughput and profitability.
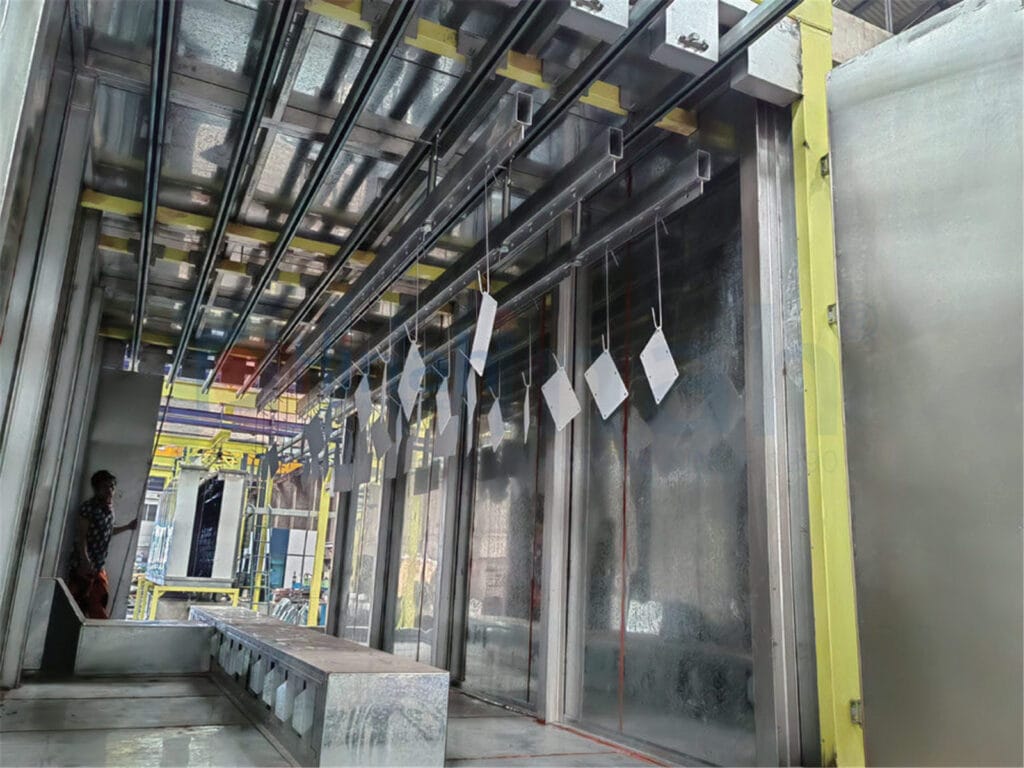
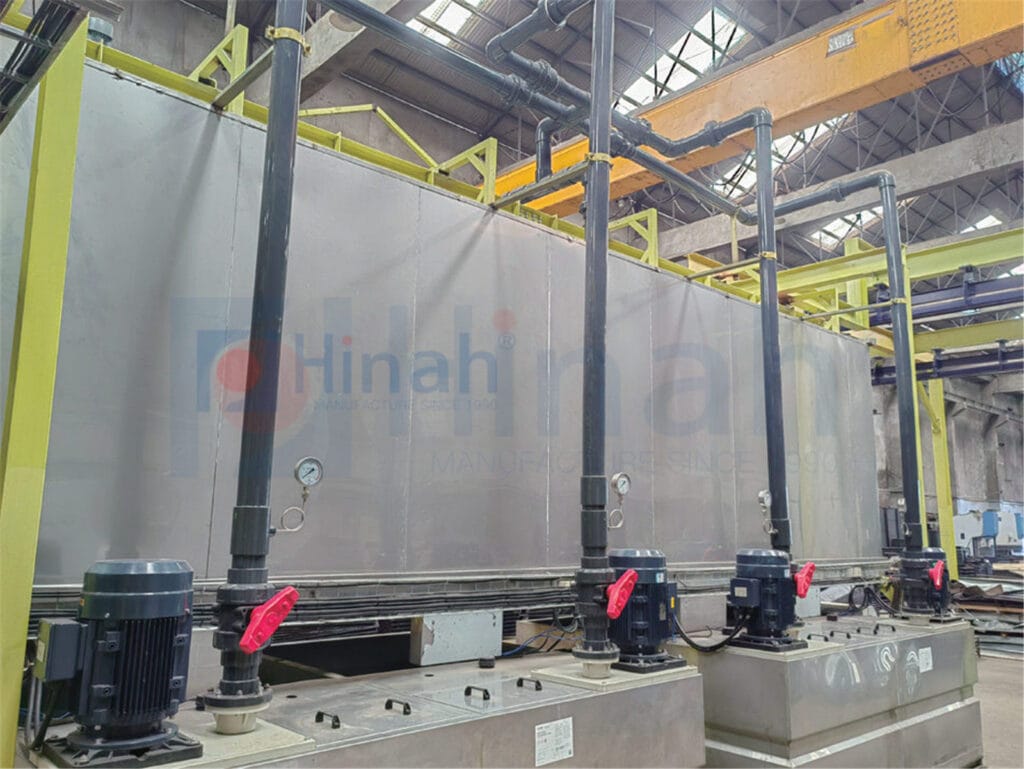
3 Ways Voltage Boosts Your Powder Coating Line Output
1. Maximizing Transfer Efficiency & Reducing Waste
Electrostatic voltage is the primary driver of transfer efficiency in your powder coating line. Higher voltage intensifies the electrostatic field, forcing more powder particles to adhere tightly to the target substrate instead of drifting as overspray. For every 10 kV increase within this optimal range, transfer efficiency can rise by 5-8%, directly slashing material waste.
This efficiency leap transforms your powder coating line economics: Reduced overspray means less frequent reclaim system maintenance, lower powder consumption per unit, and minimized disposal costs. Ultimately, voltage optimization turns wasted material into measurable profit—boosting your line’s yield without additional capital investment.
2. Accelerating Production Speeds
In high-volume environments, voltage controls your powder coating line’s rhythm. At 80-100 kV, the enhanced electrostatic pull accelerates powder deposition rates by 15-20% compared to sub-60 kV operations. This allows faster conveyor speeds or reduced pass counts—compressing cycle times without compromising coverage.
The ripple effect is profound: Shorter curing queues, increased daily throughput, and quicker job changeovers. For batch producers, this translates to 10-15% more units coated per shift. By eliminating voltage bottlenecks, your powder coating line achieves true speed scaling.
3. Ensuring Consistent Coating Quality
Voltage stability is the guardian of output consistency in your powder coating line. Fluctuations below 60 kV cause weak adhesion and orange peel, while spikes above 100 kV trigger back-ionization craters. Both scenarios force rework—halting production and slashing usable output.
Precise voltage control delivers uniform film thickness, first-pass quality rates above 98%, and near-zero reject batches. This reliability lets your powder coating line operate at peak capacity—transforming voltage from a variable into a pillar of predictable productivity.
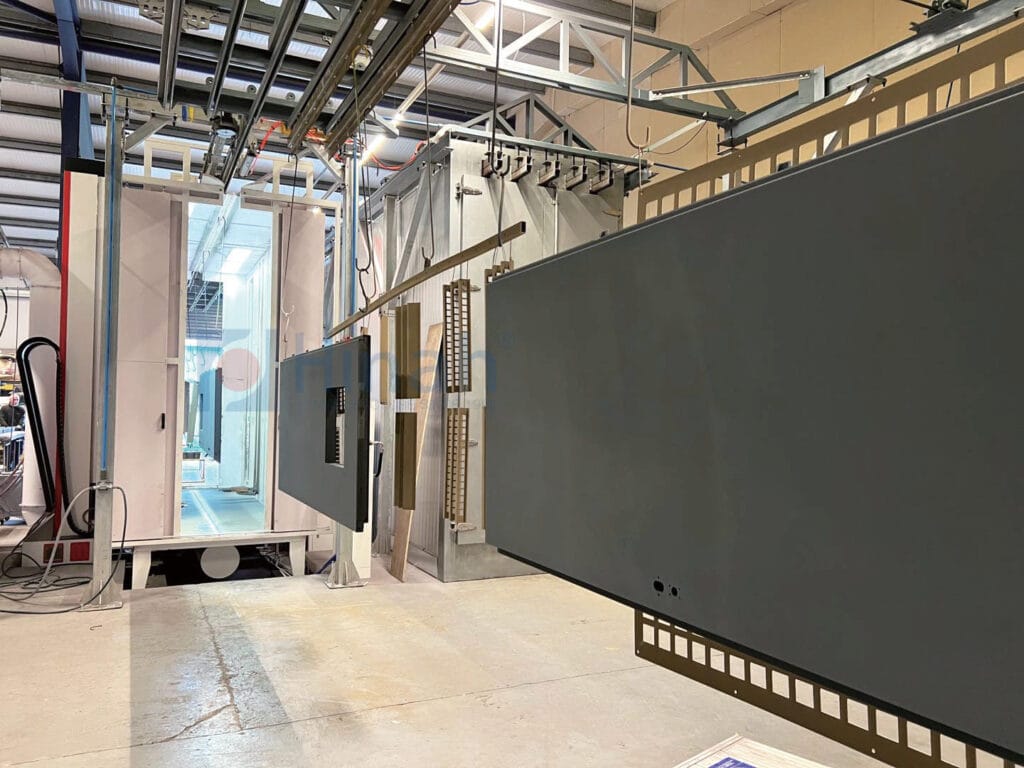
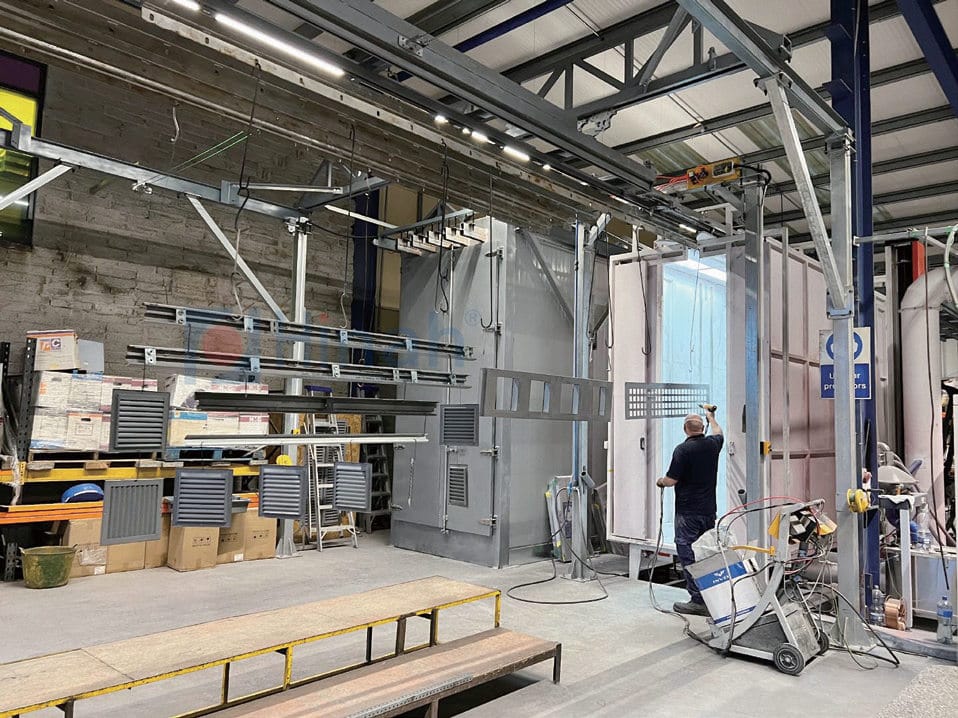
Voltage Optimization Tips for Your Coating Line
1. Steer Clear of the Under-Voltage Trap (<60 kV)
Operating below 60 kV sabotages your powder coating line’s efficiency, causing weak powder adhesion that forces re-sprays and extended cure cycles – inflating costs and throttling throughput. Counter this by deploying real-time voltage monitors with alarms; if readings dip below 60 kV, pause production to inspect grounding or gun emitters, preventing costly slowdowns and maintaining baseline output.
2. Lock in the 80–100 kV Sweet Spot for Peak Output
Consistent 80–100 kV operation is essential for high-yield powder coating lines, maximizing transfer efficiency while avoiding back-ionization defects from voltage spikes. Automate stability with self-adjusting voltage controllers (AVC) calibrated quarterly to ±2 kV tolerance, and program part-specific presets – slashing rework by 20% and unlocking your line’s true capacity.
3. Build Voltage Resilience into Line-Wide Systems
Voltage optimization extends beyond the gun: ensure whole-powder coating line synergy through monthly ≤1 ohm grounding audits, controlled booth airflow, and 45–55% humidity management. This integrated approach prevents environmental charge loss, transforming your line into a predictable, high-output asset.
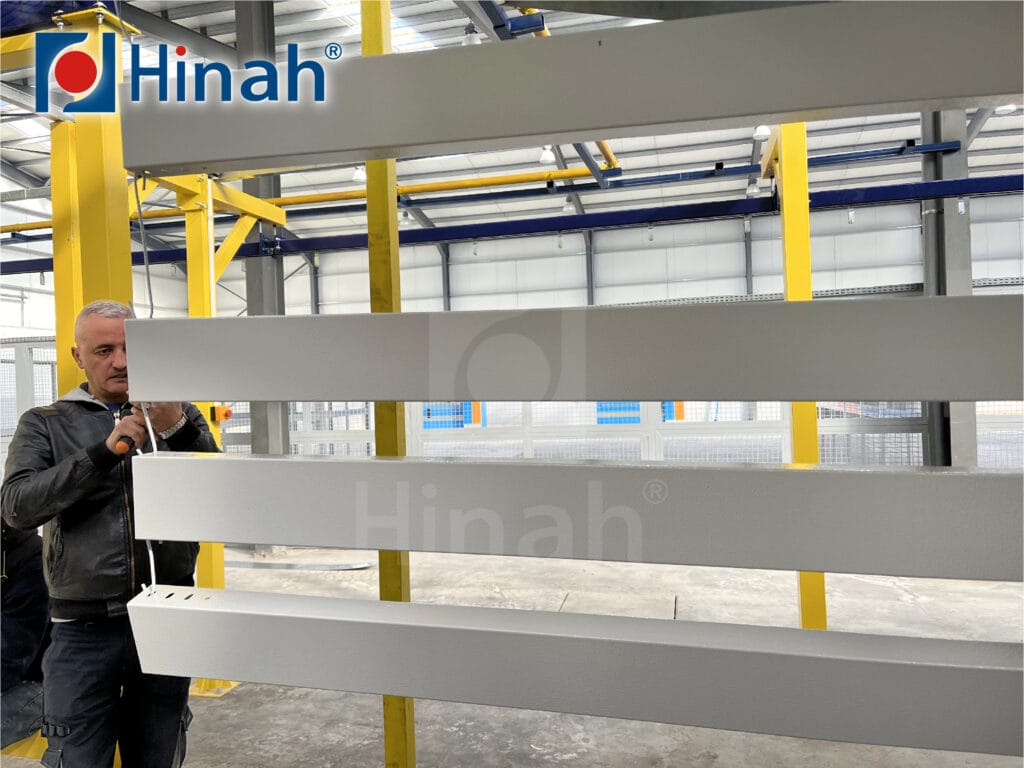
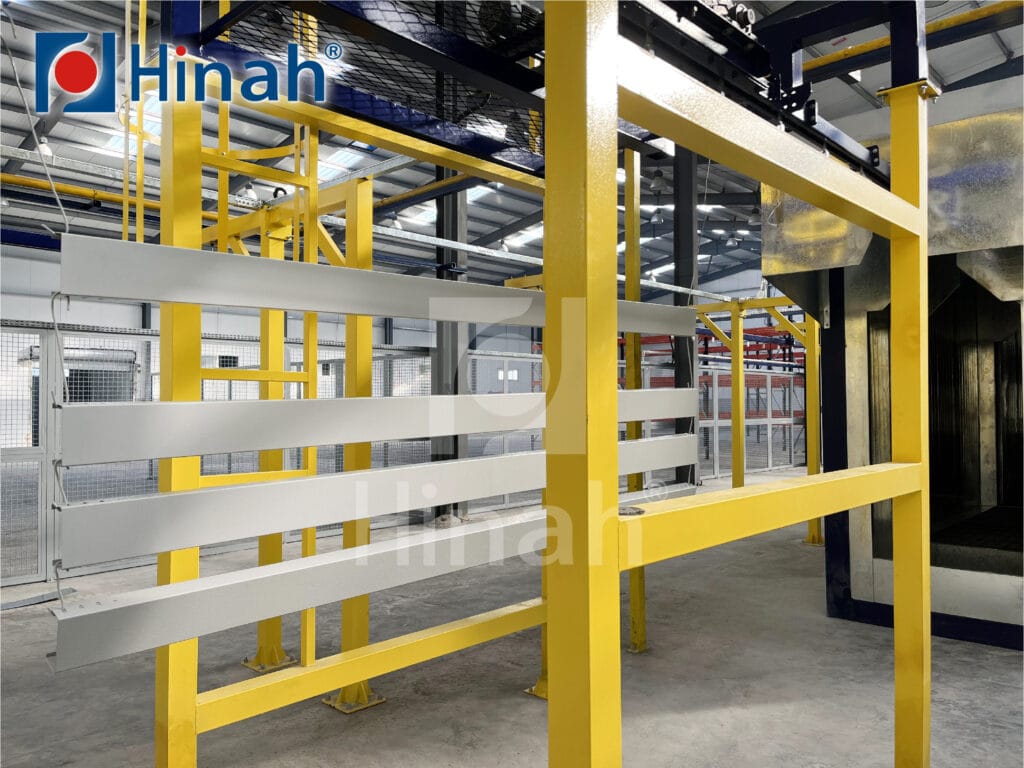
Conclusion
Electrostatic voltage is far more than a technical setting—it’s the strategic lever for maximizing your powder coating line’s output. By maintaining the sweet spot, you directly boost transfer efficiency, accelerate production cycles, and eliminate quality-related downtime. This transforms voltage from a hidden variable into a measurable driver of throughput and profitability. Audit your powder coating line’s voltage parameters today—unlock 10–15% higher yield without capital investment, turning optimized electrostatics into your competitive edge.