Shrinkage holes – those tiny craters marring your powder-coated surfaces – are more than cosmetic flaws. They sabotage product quality, trigger customer rejections, and silently bleed profits from your powder coating line. Often dismissed as random defects, these “fish eyes” (as they’re known in the industry) actually signal systematic contamination or process failures within your coating operation.
The truth is simple: shrinkage holes don’t occur by chance. They erupt when incompatible substances invade the coating process, causing the liquefied powder to violently retract. Left unchecked, they force costly rework and undermine your brand’s reputation for durability. But here’s the good news: eliminating them is achievable. By targeting four root causes specific to industrial powder coating lines, you can reclaim defect-free finishes and predictable production. Let’s expose this hidden enemy.
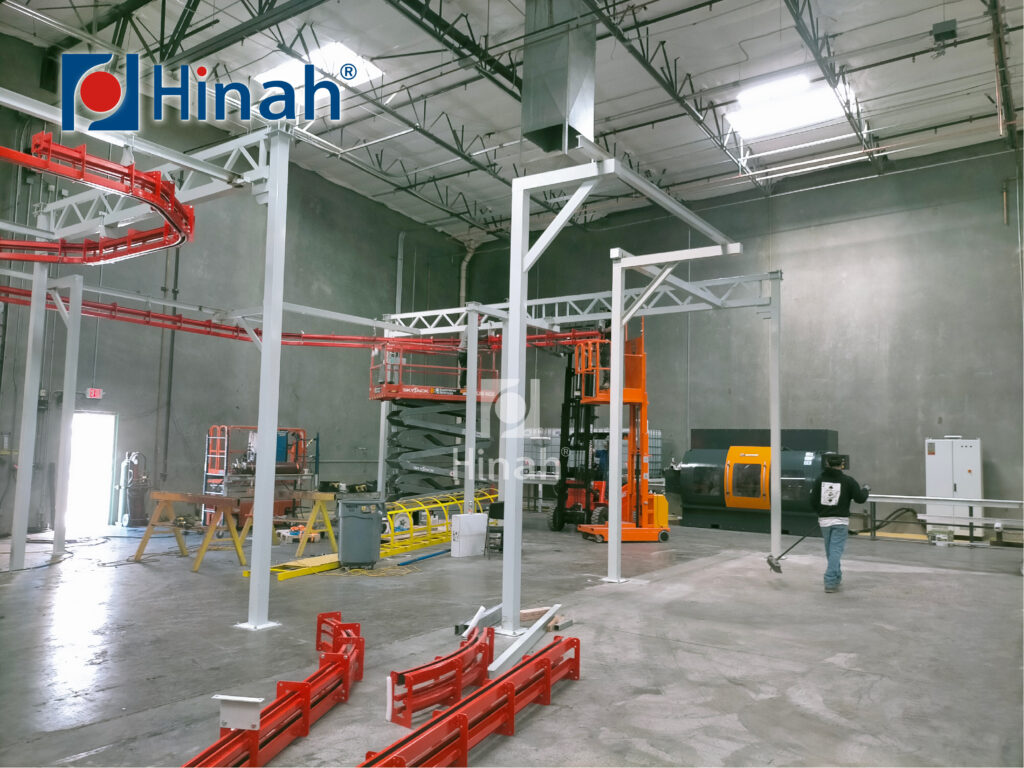
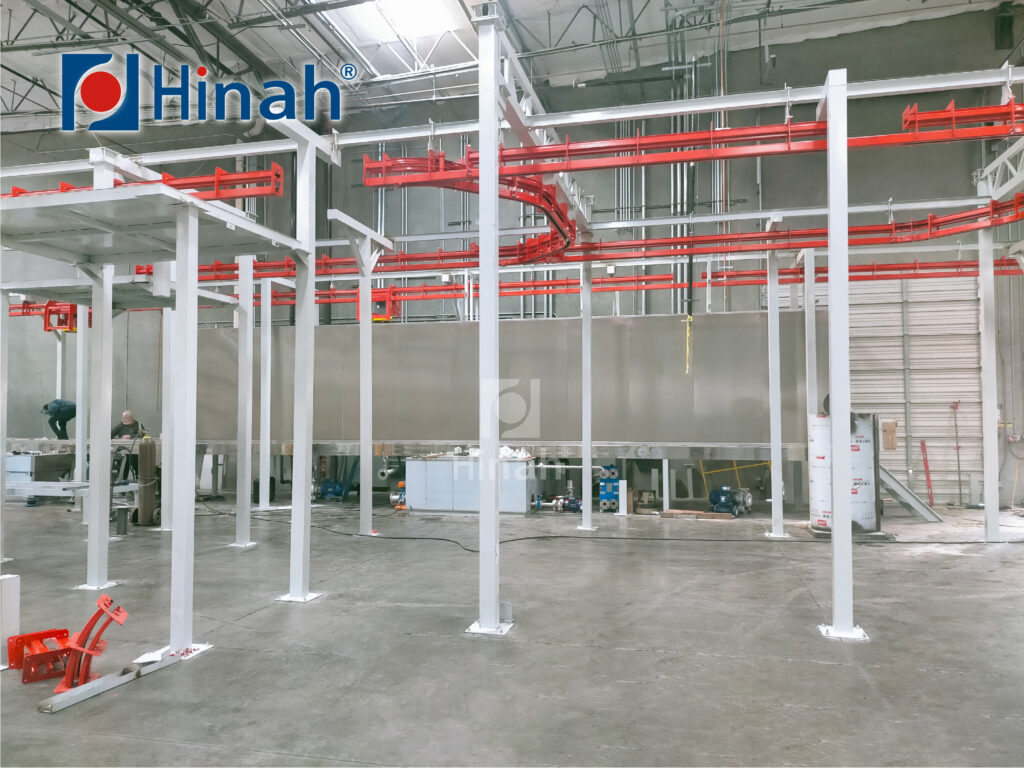
I. The “Fish Eyes” Sabotaging Your Powder Coating Line
Shrinkage holes (industry term: “fish eyes”) are micro-craters (0.1-2mm diameter) that erupt on coated surfaces, resembling tiny volcanic pits. These defects occur when contaminants on your powder coating line – oils, silicones, or moisture – create localized surface tension gradients, causing the molten powder to violently retract during curing. Unlike pinholes (trapped air), fish eyes form distinct circular voids with raised edges, exposing bare substrate and compromising corrosion protection. On production lines, they cluster near conveyor contact points or airflow zones – clear markers of systemic contamination.
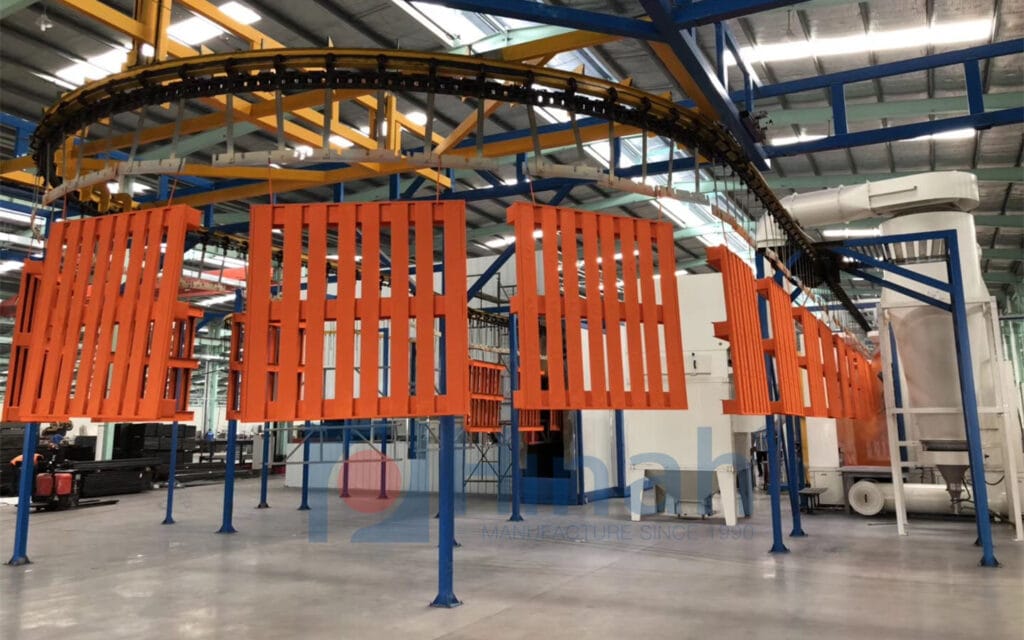
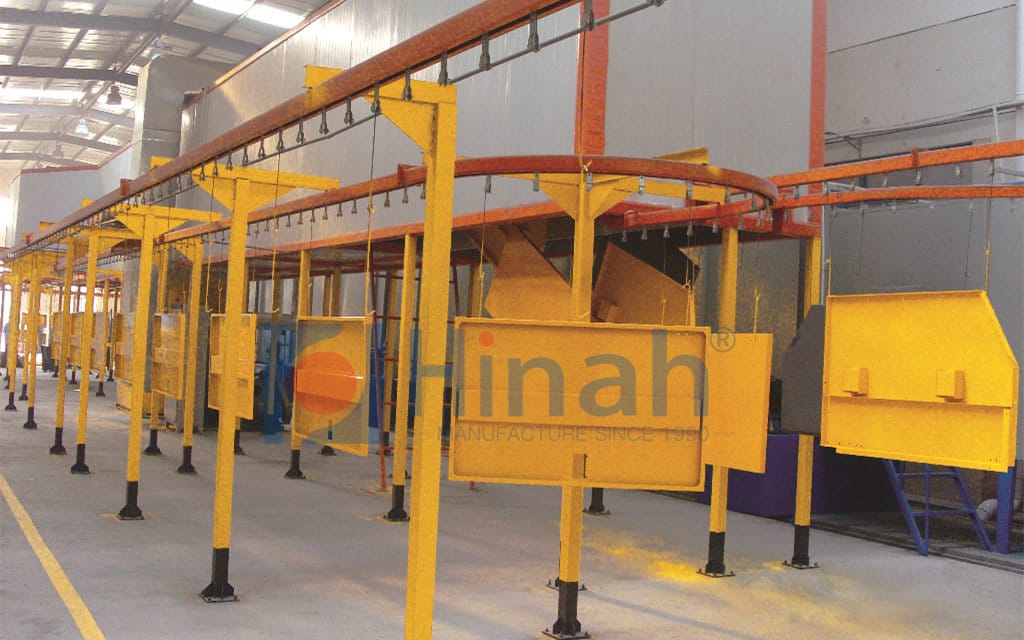
II. Why Shrinkage Holes Occur in Your Powder Coating Line
Shrinkage holes aren’t random flaws – they’re symptoms of specific contamination failures in your powder coating process. Here’s how four critical breakdowns trigger this costly defect:
2.1 Conveyor Chain Contamination: The Invisible Oil Rain
Unsealed bearings or excessive lubricant on your powder coating conveyor system release oils that turn into airborne droplets. Carried by oven airflow, these contaminants land on substrates, creating invisible barriers. When powder melts during curing, it violently retracts from these oily spots, forming perfect circular craters. High-risk areas include conveyor junctions and sections near air intake vents.
2.2 Powder Degradation: Humidity & Mixing Hazards
When powder in your coating line absorbs moisture (common in humid environments), it clumps and loses fluidity. This compromised powder acts like a surfactant during curing, forcing localized shrinkage. Similarly, accidental mixing of incompatible powder types – like polyester and epoxy – causes chemical conflicts that manifest as fish eyes, even from minor cross-contamination.
2.3 Pre-treatment Failures: The Dirty Secret
Inadequate degreasing or contaminated rinse water on your powder coating line leaves invisible residues (oils or surfactants) on metal surfaces. These residues repel liquid powder during the melt phase, like water on a waxed car. The result? Powder coating shrinks away from contaminated zones, leaving exposed craters exactly where protection is needed most.
2.4 Tainted Utilities: Water & Air Betrayal
Moisture-laden compressed air spraying from guns delivers tiny water droplets onto freshly coated surfaces. These droplets “poison” the powder, triggering immediate shrinkage as they vaporize during curing. Similarly, oily process water leaves micro-residues during rinsing that later sabotage coating adhesion. Both failures cluster near spray booths and blow-off stations in industrial coating lines.
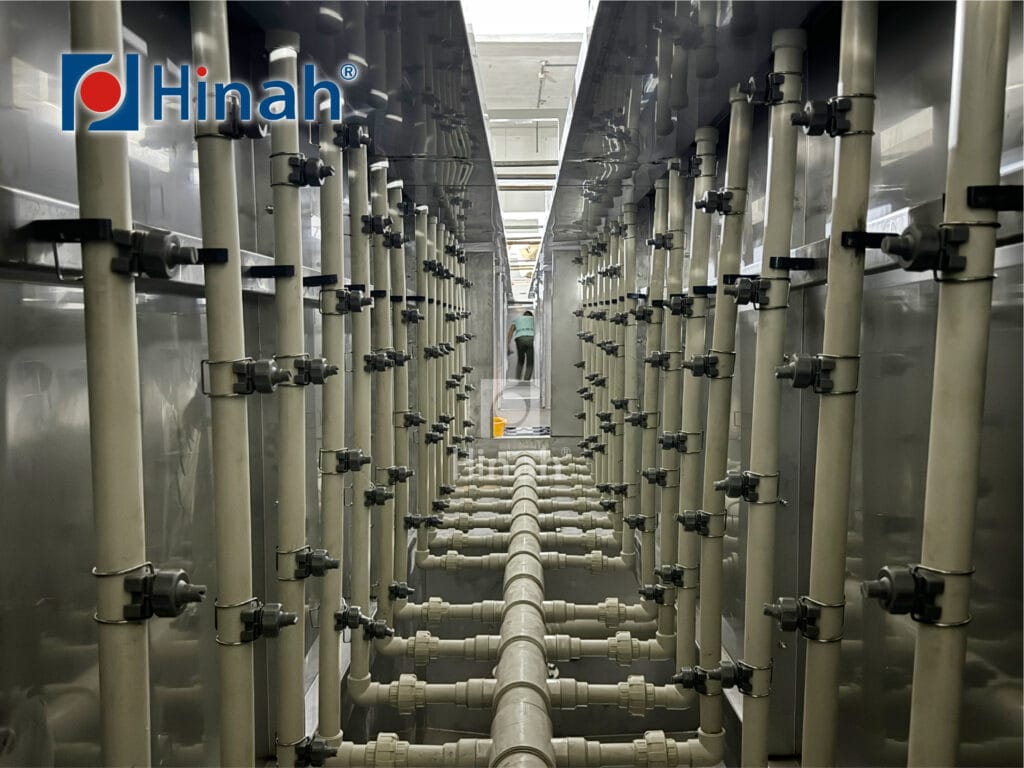
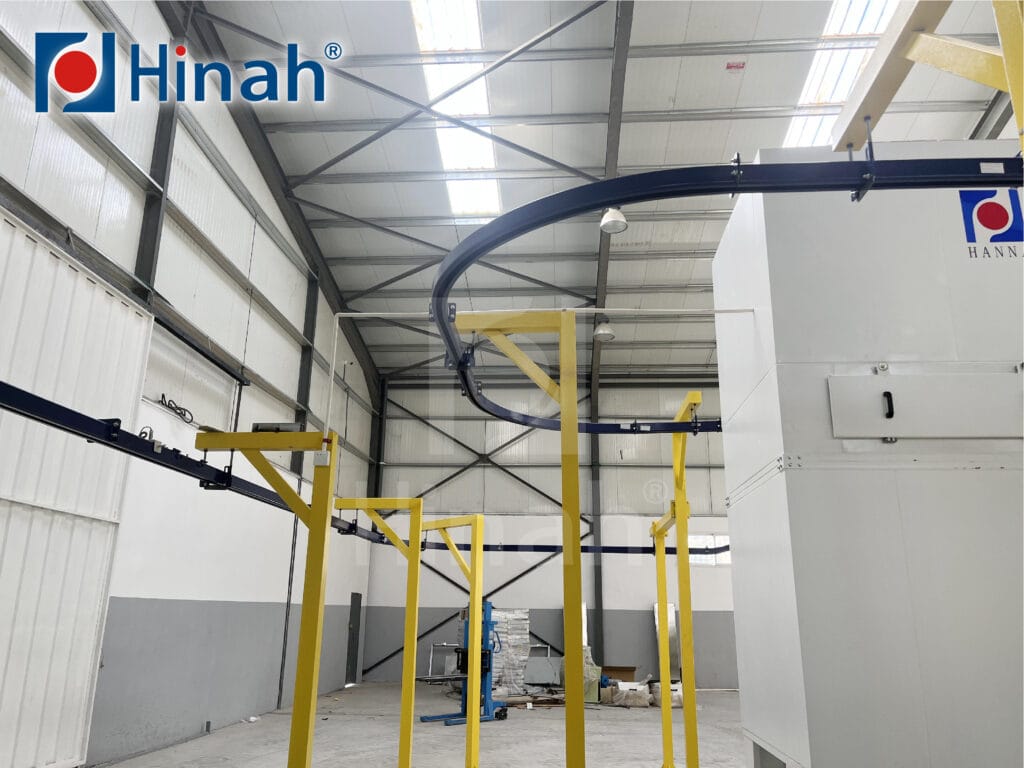
III. Battle-Tested Solutions for Your Coating Line
Stop chasing symptoms – attack the roots. These field-proven fixes eliminate shrinkage holes by purging contamination at its source in your powder coating line:
- Neutralize conveyor oils decisively. Mandate daily wipe-downs of chains and bearings using specialized silicone-free cleaners – this erases airborne oil risks. For lines with strong airflow, install redirect shields near oven intakes to block contaminated gusts from reaching parts. Switch to low-mist lubricants and enforce a “less-is-more” greasing policy. Remember: clean chains need far less lubrication.
- Lock down powder integrity. Store all powders in rigorously sealed containers kept consistently cool and dry. Never allow different powder types to mingle – assign dedicated recovery systems and tools per formulation. Integrate moisture-trapping breathers on storage hoppers and screen recycled powder through ultra-fine sieves to crush clumps before reuse.
- Transform pre-treatment into a fortress. Automate concentration checks for degreasing tanks to maintain peak effectiveness without over-etching metal. Use purified water for final rinses and monitor cleanliness relentlessly – if water leaves streaks or residues, halt and purge. Filter swaps and tank cleaning must be non-negotiable weekly rituals.
- Purge utilities with zero mercy. Equip compressed air lines with industrial-grade moisture crushers that extract water and oil before air touches powder. Drain tanks after every shift without fail. For process water, deploy multi-stage filtration systems that annihilate contaminants at every level. Spot any grime near spray guns? That’s your red alert to overhaul utilities.
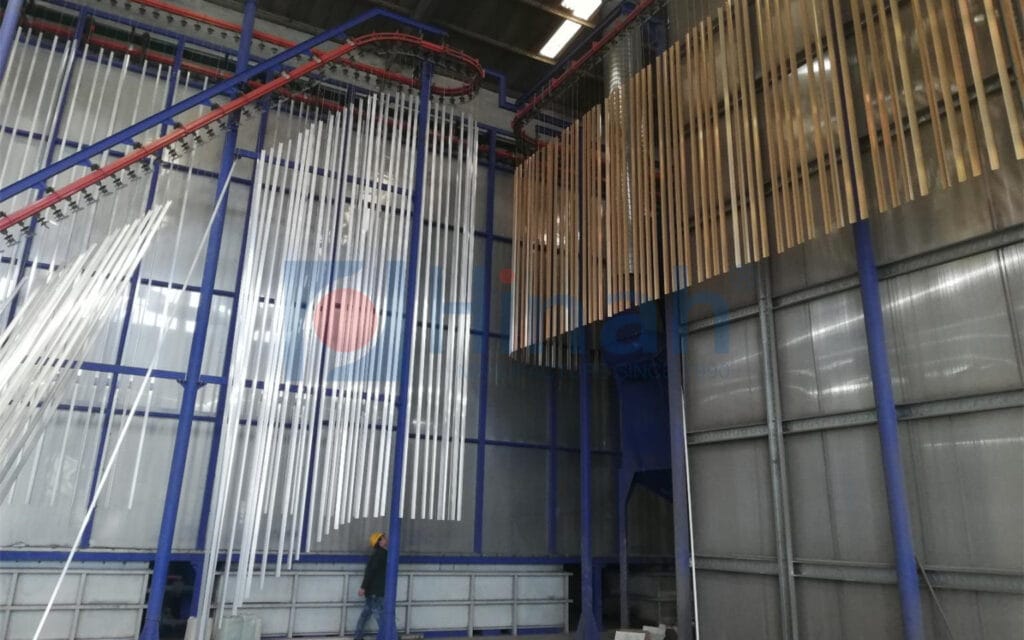
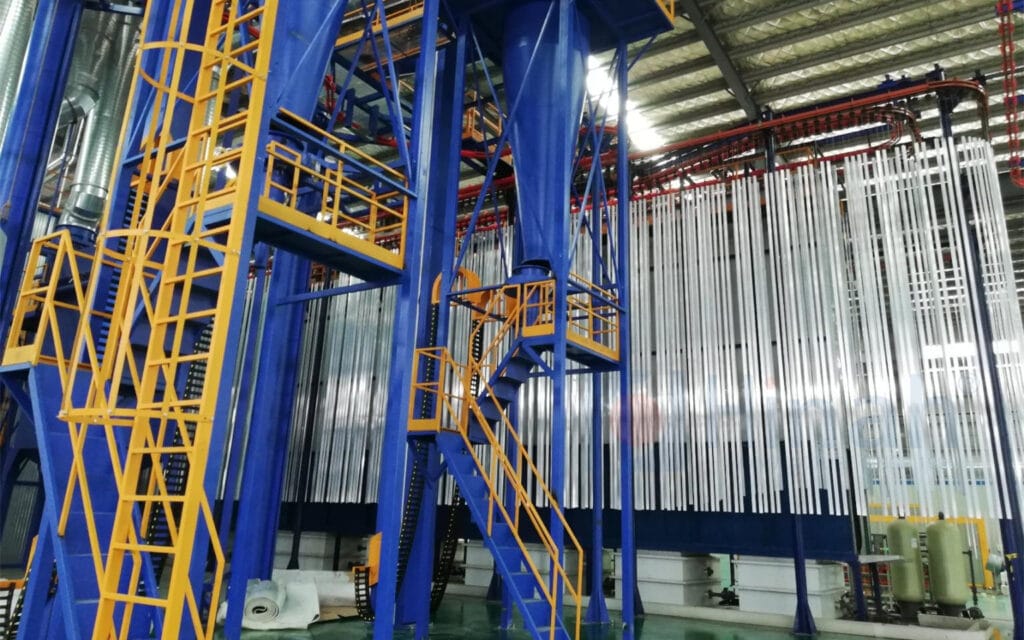
IV. Conclusion
Shrinkage holes in your powder coating line are not inevitable – they’re conquerable signals of contamination. By executing the targeted strategies outlined here, you transform vulnerability into dominance: clean chains defeat oil rain, disciplined powder management suffocates humidity, fortified pre-treatment annihilates residues, and purified utilities crush hidden saboteurs. This systematic purge of contamination sources doesn’t just erase fish eyes – it forges a foundation for zero-defect production.