The power and free conveyor system is the essential framework for complex industrial transport. Its core principle is simple yet powerful: separate the continuously moving drive chain from independently controllable load carriers. This decoupling enables precise stopping, accumulation, and routing – delivering unmatched flexibility critical for modern, high-mix manufacturing.
This capability makes P&F the backbone of efficient automatic powder coating line. It seamlessly moves parts through harsh environments like spray booths, ovens, and workstations – handling dust, overspray, and heat while ensuring precision positioning. For coating lines demanding reliability and adaptability, understanding the P&F system’s components is fundamental to performance.
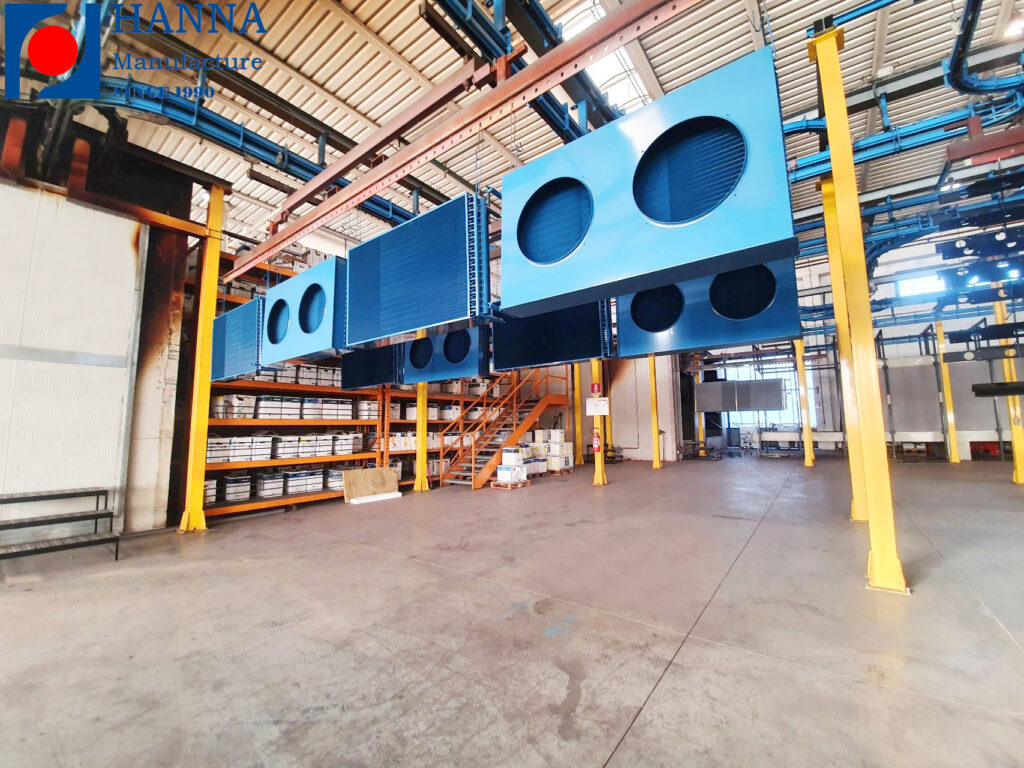
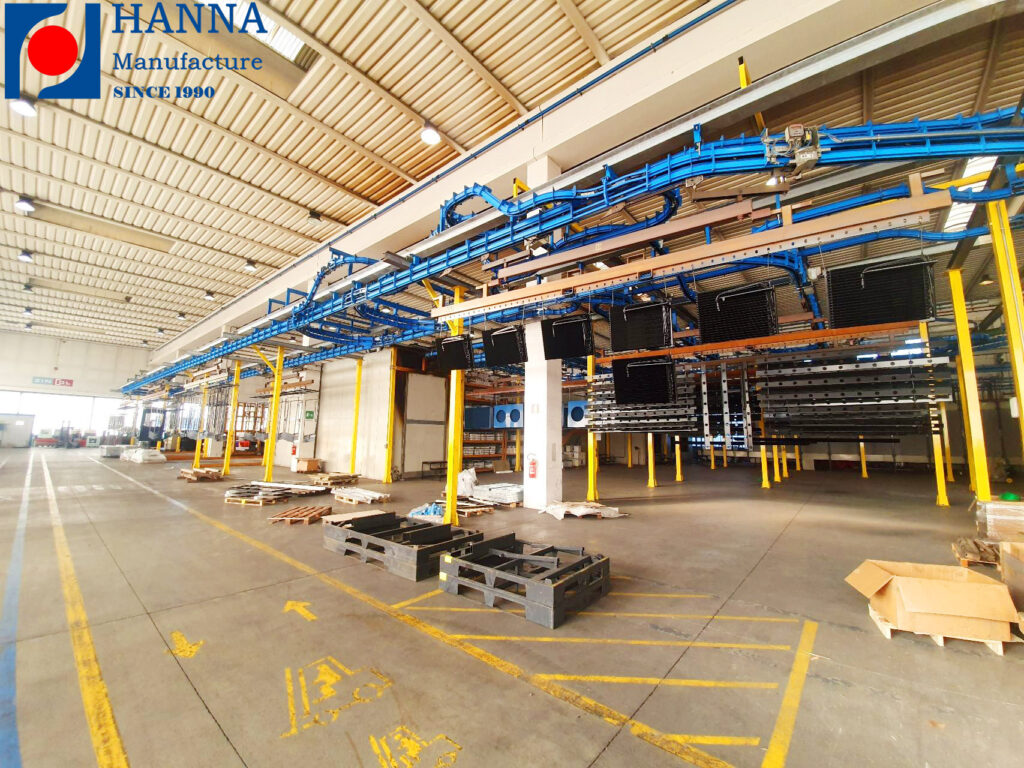
I. How a Power and Free Conveyor System Works
The power and free conveyor system operates on a simple yet ingenious principle: decoupling transport speed from workstation processing time. A continuously moving drive chain (the power element) runs along a dedicated track, while load carriers travel on adjacent accumulation tracks (the free element). Key to this system are pusher dogs attached to the drive chain, which selectively engage with lugs on the carriers. When engaged, carriers move with the chain’s speed; when disengaged (typically via mechanical lifts or switches), carriers stop or accumulate independently – allowing workpieces to pause for spraying, curing, or inspection without halting the entire line. This unique engage/disengage mechanism enables precise zone control, variable speeds between processes, and seamless buffering, making it indispensable for synchronizing complex sequences in automatic powder coating line where uninterrupted flow through powder coating booth, powder coating oven, and workstations is critical.
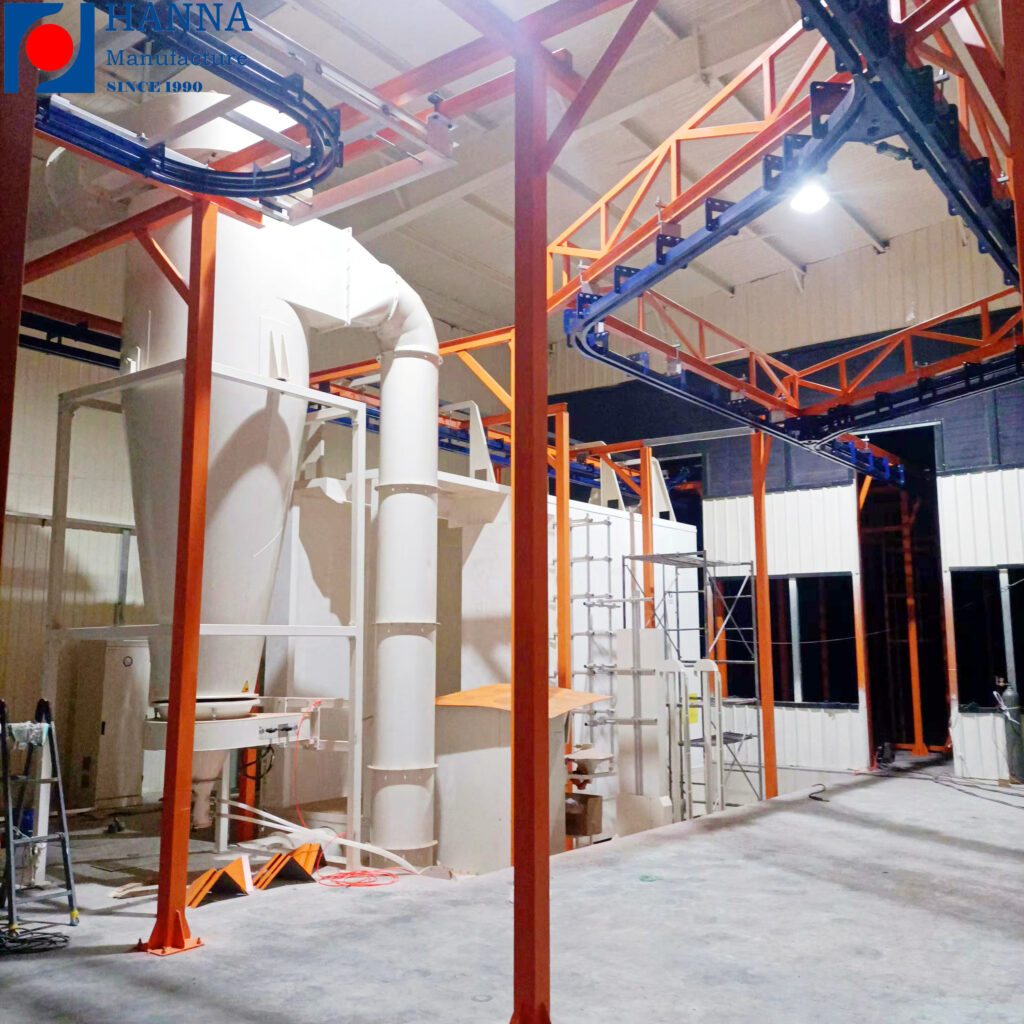
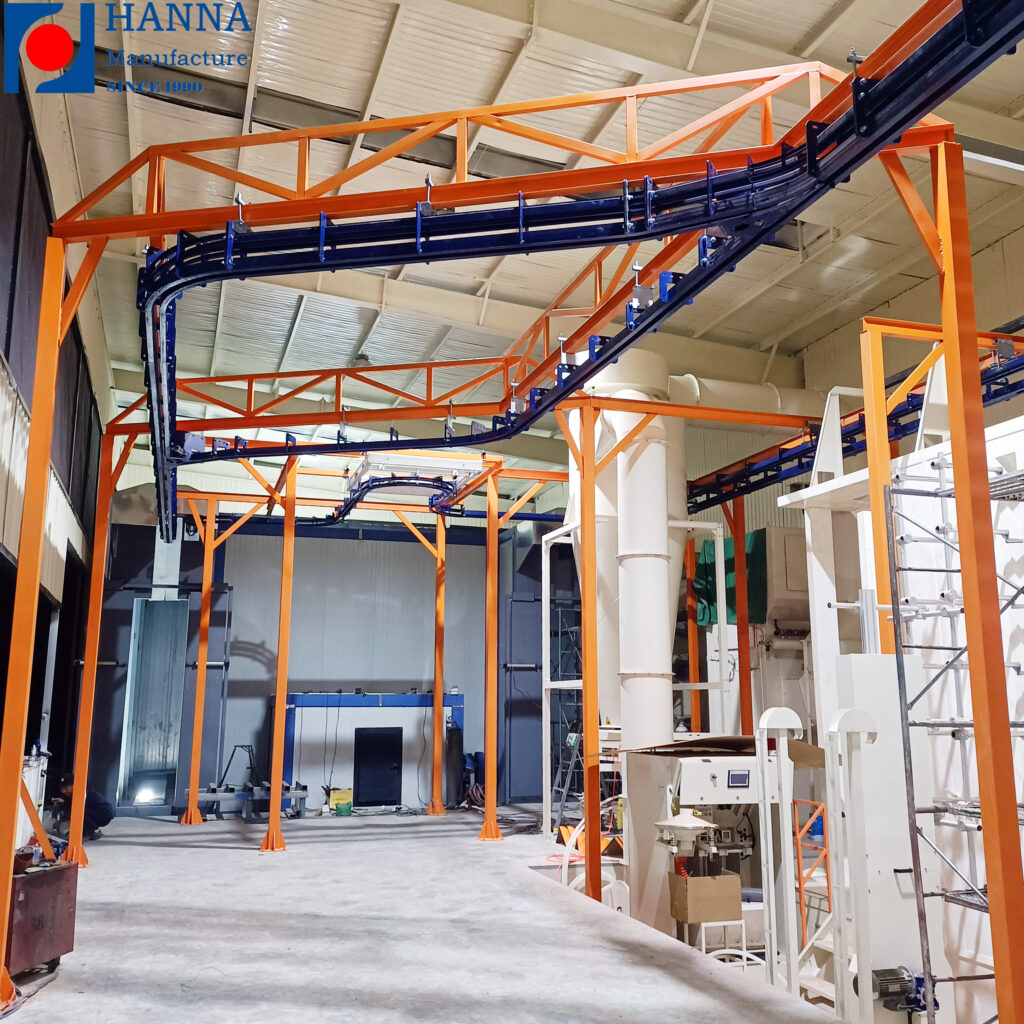
II. Deconstructing the Power and Free Conveyor System
A robust power and free conveyor system for demanding applications like automatic powder coating line comprises precisely engineered components. Each plays a critical role in ensuring resilience, precision, and operational flexibility:
Structural Foundation & Tracks
1. Steel Framework: Heavy-duty support structure engineered for stability, thermal expansion tolerance near ovens, and long-span integrity.
2. Accumulation/Main Tracks:
Dual-path design:
- Power Track: Channels the continuously moving drive chain.
- Free Track: Allows independent carrier stopping/accumulation.
Propulsion & Drive System
1. Drive Units: High-torque, variable-speed motors with sealed enclosures to resist dust, overspray, and oven heat. Ensure reliable start-stop operation.
2. Traction (Drive) Chain: Heavy-duty, wear-resistant chain moving continuously. Engages carriers via pusher dogs. Built to withstand chemical exposure and abrasion.
3. Tensioners: Automatic or manual take-ups maintain optimal chain tension, preventing slippage and premature wear.
Load Handling & Positioning
1. Load Carriers (Trolleys):
- Robust frames supporting ≥150kg loads at workstations (spraying, putty, sanding).
- Feature lugs for drive chain engagement/disengagement.
- Harsh-Environment Design: Easy-clean surfaces, heat-resistant materials, optional rotators for coating access.
2. Stops & Workstations:
- Precision pneumatic/hydraulic stops position carriers.
- Integrated ≥150kg Capacity Movable Platforms at spray, putty, and sanding stations for operator ergonomics and part access.
Routing Control
Switches (Turnouts): Mechanically divert carriers between tracks (e.g., into ovens, repair zones). Pneumatic/electric actuation with high-reliability design to prevent jams in critical paths.
Control, Safety & Integration
1. Control System (PLC/HMI):
- Dual Control Modes: Seamless Manual/Automatic operation for flexibility.
- Reliability & Diagnostics:Low fault rate; clear Chinese/English alarm displays; fault bypass capability for manual continuation.
- Spray Program Management: Easy storage, recall, editing, and modification of recipes for different products.
- Communication:Ethernet interfaces for SCADA/MES integration; ≥20% spare I/O points.
- Usability: Intuitive HMI requiring minimal operator training.
2. E-Stop System: Strategically placed emergency stop buttons triggering immediate safety shutdowns.
3. Sensors: Position/presence detection units rated for harsh environments.
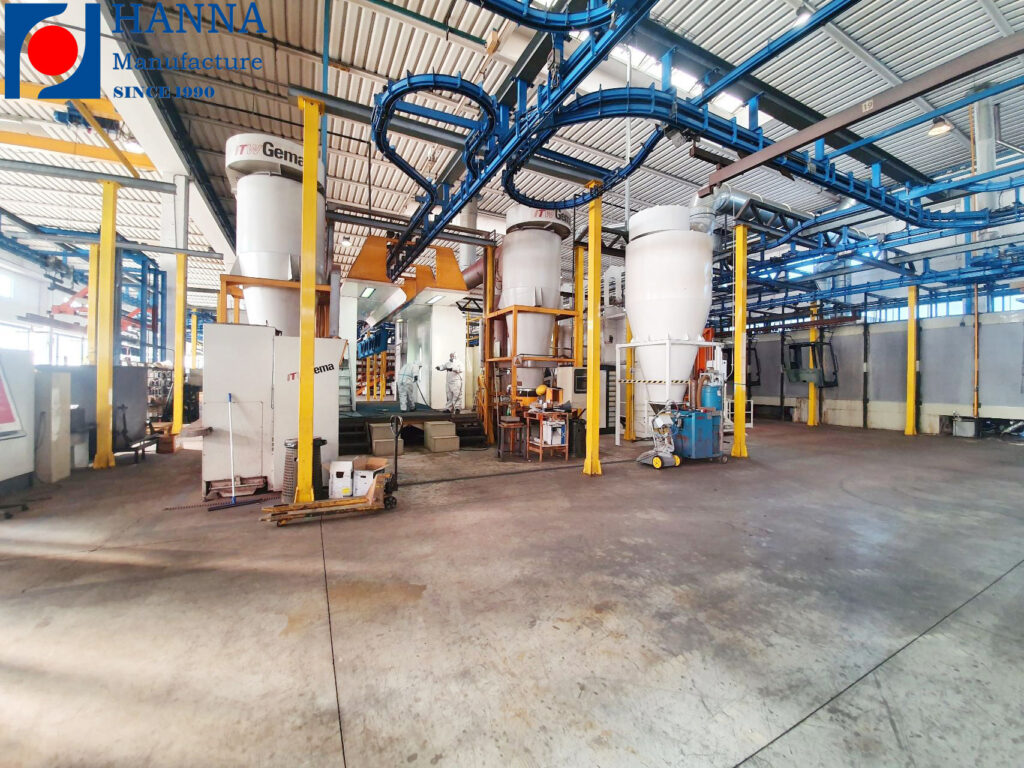
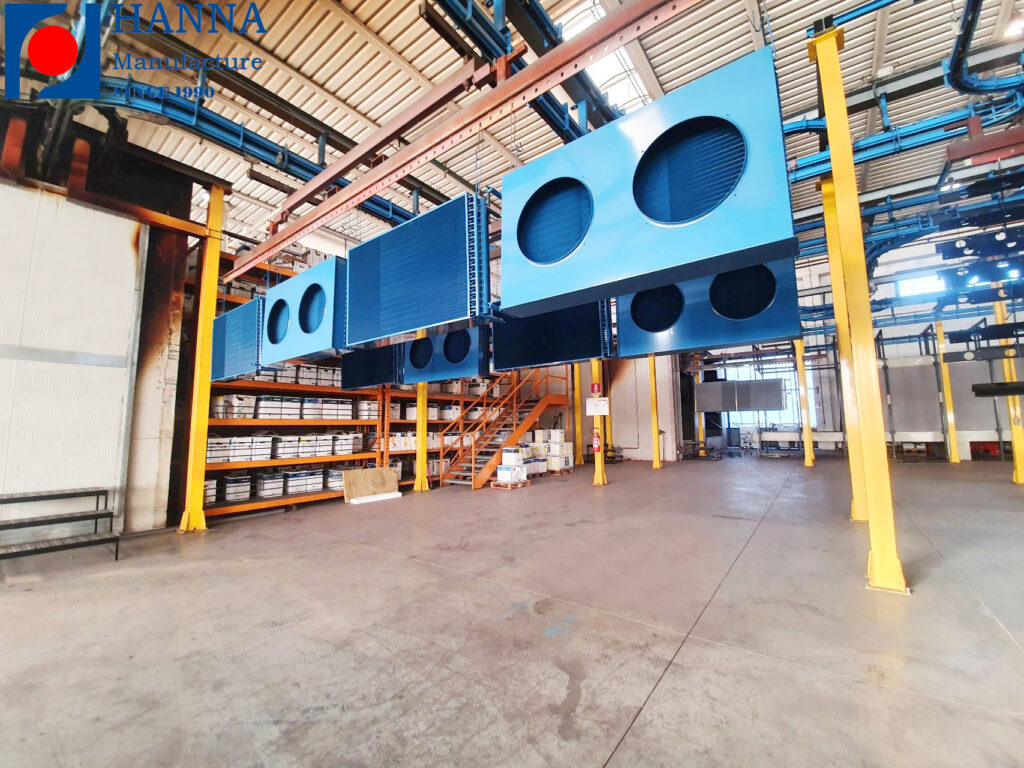
III. Why the Power and Free Conveyor System Excels in Powder Coating Line
The Power and Free Conveyor System is unmatched in automatic powder coating lines due to its inherent adaptability to complex, demanding environments:
- Harsh Environment Mastery: Components like easy-clean tracks, sealed drive units, and resistant carriers withstand overspray, dust, and oven heat while simplifying maintenance.
- Precision Workflow Control: Independent carrier stopping/accumulation allows parts to pause for spraying, curing, or inspection without disrupting line flow – synchronizing perfectly with variable process times.
- Heavy-Duty Flexibility: Robust carriers and integrated movable platforms (≥150kg capacity) handle heavy workpieces effortlessly at spray, putty, and sanding stations.
- Intelligent & Resilient Operation: The PLC control system enables manual/auto modes, provides clear Chinese alarms, allows fault bypass, and supports easy program editing – all with 20% I/O spare and Ethernet connectivity for future-ready integration.
Simply put, P&F delivers the reliability, precision, and smart control essential for high-yield, low-downtime coating operations.
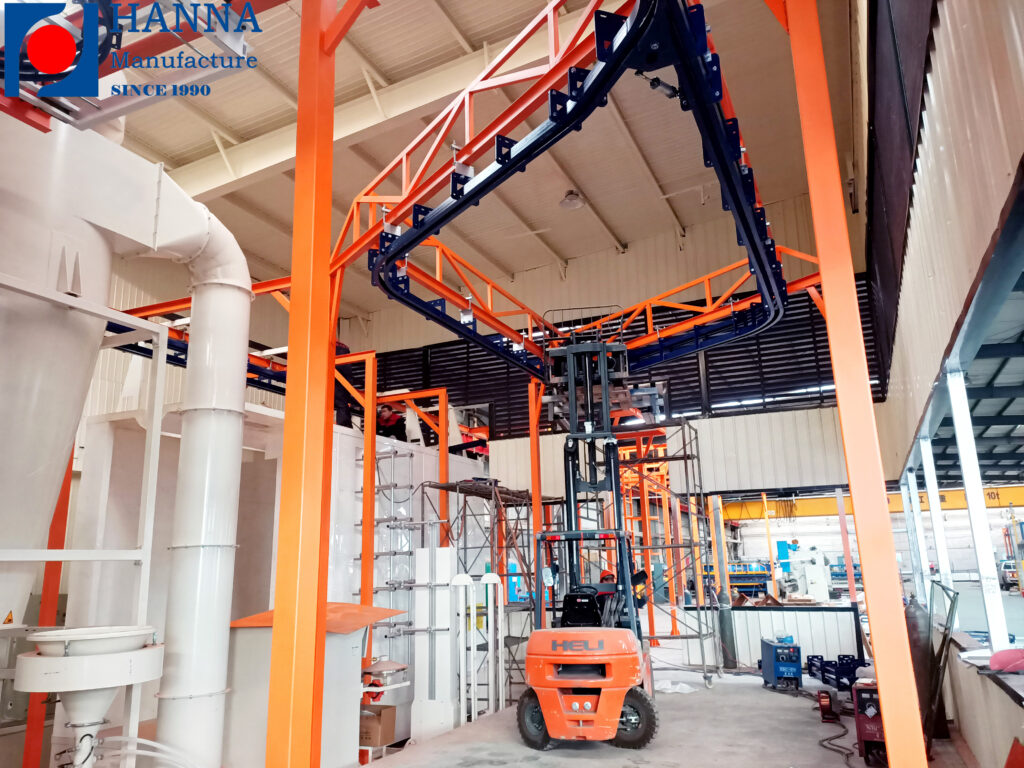
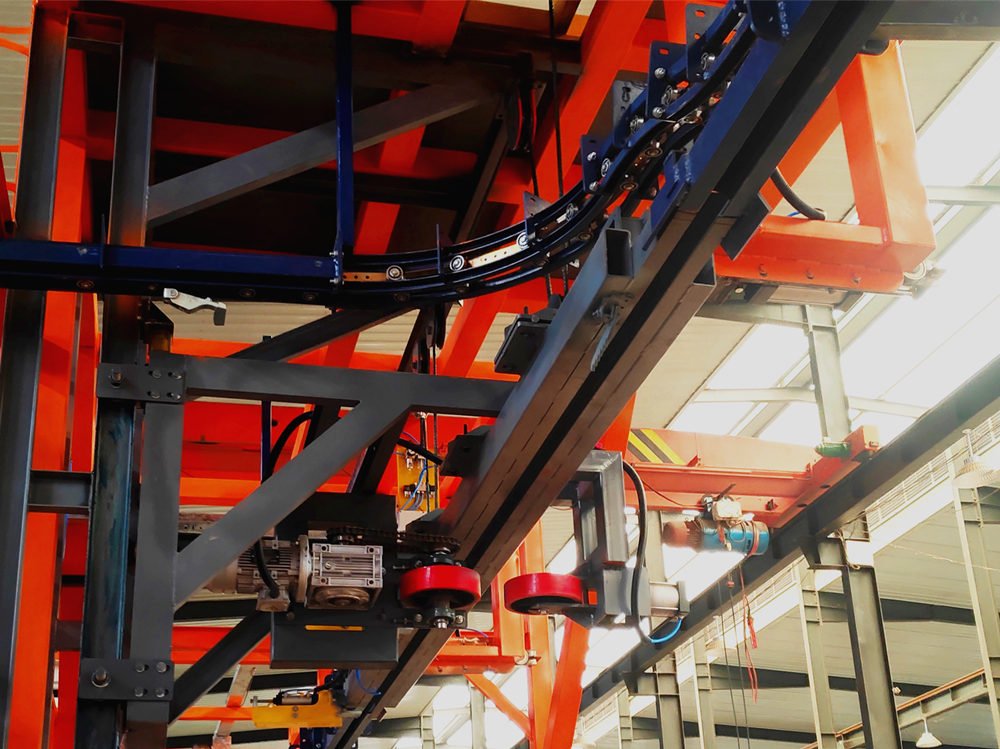
V. Conclusion
In summary, the power and free conveyor system delivers unparalleled efficiency for automatic powder coating lines by harmonizing purpose-built components. This synergy ensures resilience against harsh environments, precise workflow synchronization, and minimal downtime through operator-friendly fault recovery. For manufacturers prioritizing throughput, quality, and operational agility, investing in a rigorously engineered P&F system isn’t just a logistical choice; it’s the foundation for a competitive, future-ready finishing operation.