Conveyor chains are the backbone of efficient powder coating line, yet their failures often trigger costly ripple effects. A single malfunction can halt production, incur unplanned repairs, and compromise coating consistency—costing manufacturers thousands in lost productivity. While these components appear simple, they demand precise alignment and tension control to maintain smooth workpiece flow. Alarmingly, over 60% of unplanned stoppages in automated coating systems stem from preventable chain issues like uneven wear, misaligned sprockets, or improper tensioning.
This article exposes the overlooked failure mechanisms behind conveyor chain breakdowns, from distorted plates causing uneven loads to critical drive sprocket misalignments. Discover why reactive fixes fail and how proactive maintenance strategies can transform these hidden vulnerabilities into opportunities for uninterrupted production and consistent finish quality.
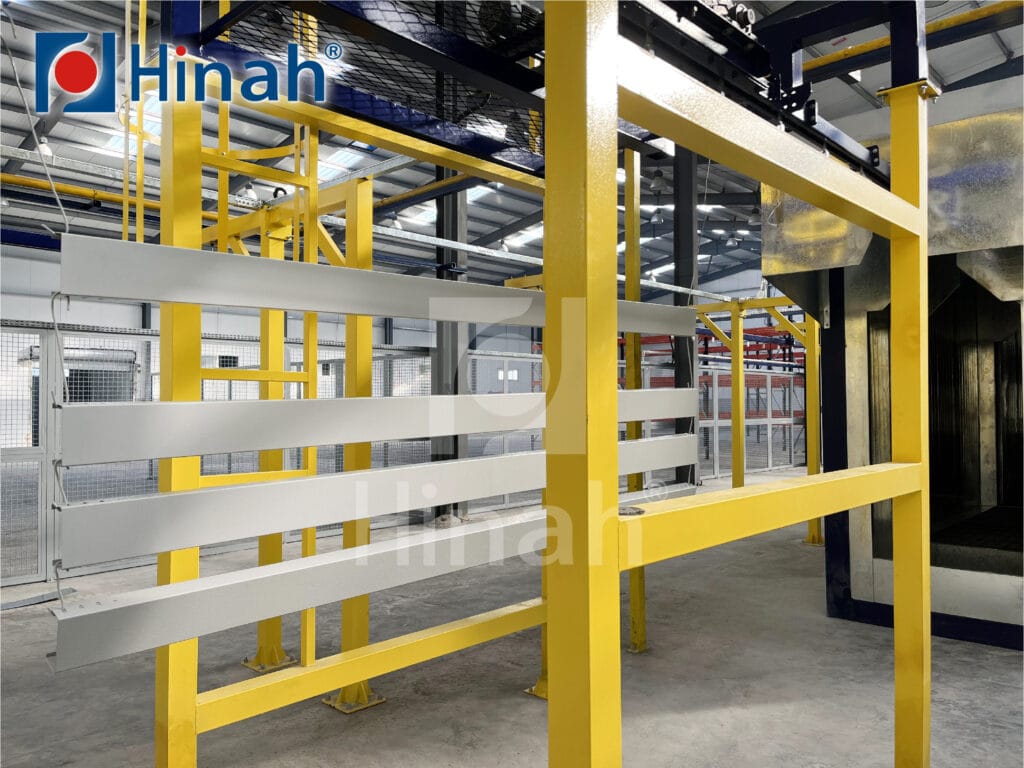
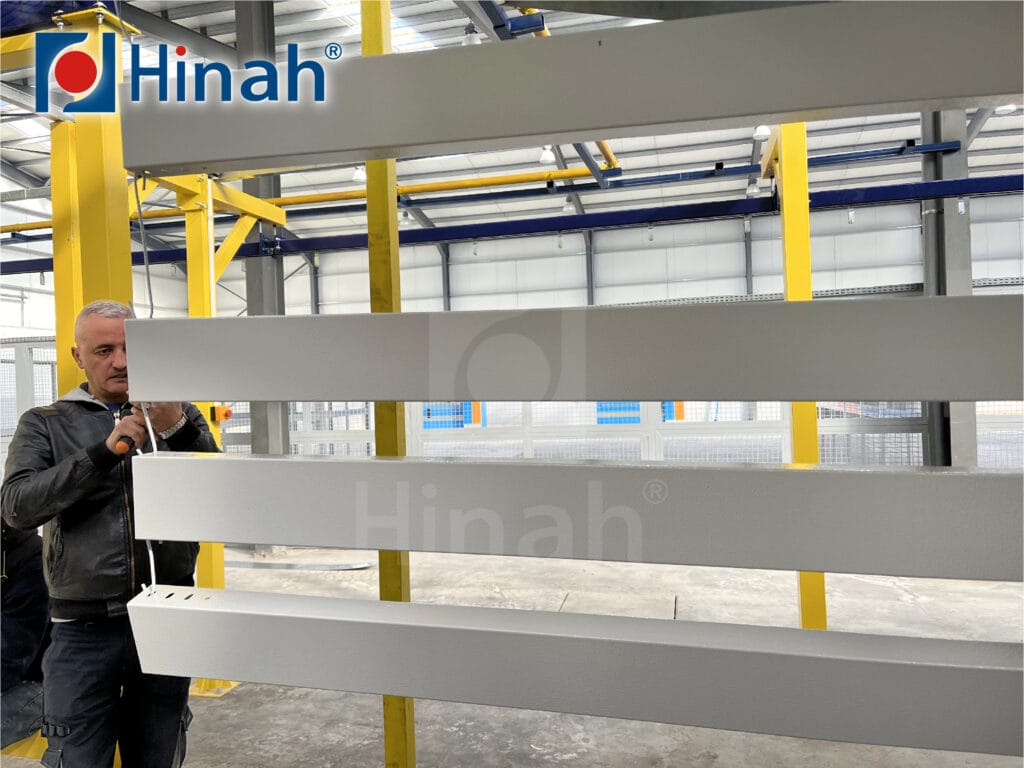
Common Conveyor Chain Failures in Powder Coating Line
- Imbalanced Chain Length & Uneven Tension
Uneven chain lengths in dual-strand powder coating line create dangerous tension imbalances, often overlooked during installation or maintenance. A mere 2-3% length mismatch forces one chain to bear over 70% of the load, accelerating wear on pins and rollers while causing visible “washboard” vibration patterns on coated surfaces. These imbalances eventually lead to chain skipping or derailment, particularly near drive sprockets. Regular laser alignment checks and tension gauges are critical to maintaining tolerance within 0.5mm/m length difference. Proactive solutions include replacing chains in pairs (never individually) and installing auto-tensioners with real-time load monitoring to prevent costly unplanned downtime.
- Worn Chain Plates & Channel Degradation
Progressive wear of chain plates and guide channels is a silent killer in high-throughput powder coating line. When plate thickness erodes beyond 1.2mm or channel grooves widen over 2.5mm, lateral sway develops—misaligning workpieces in coating booths and leaving telltale metal shavings in lubrication systems. Hardened steel plates (HRC 50+) paired with tungsten-disulfide dry lubricants can extend service life by 300%, while monthly wear mapping using digital calipers helps identify hourglass-shaped thinning at pivot points before catastrophic failures occur.
- Thermal Warping & Chain Plate Deformation
The extreme heat of curing ovens (180-220°C) causes differential expansion in standard chains, shrinking effective pitch by 0.8mm/m and triggering “snaking” movements that shear pins and disrupt coating consistency. Chains operating in thermal zones should exhibit less than 1.5mm pitch variation across 10 links—a threshold easily monitored with infrared cameras during curing cycles. Heat-treated chains rated for -40°C to 250°C, combined with strategic expansion joints every 6m in oven sections, mitigate warping while maintaining precise workpiece positioning through temperature fluctuations.
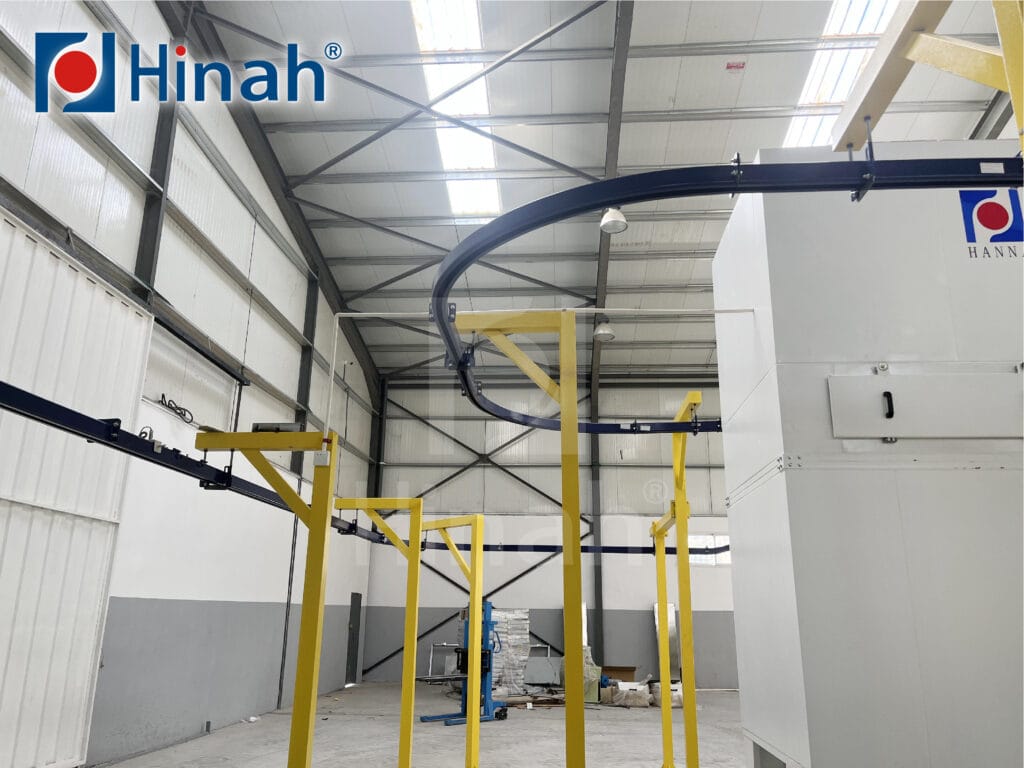
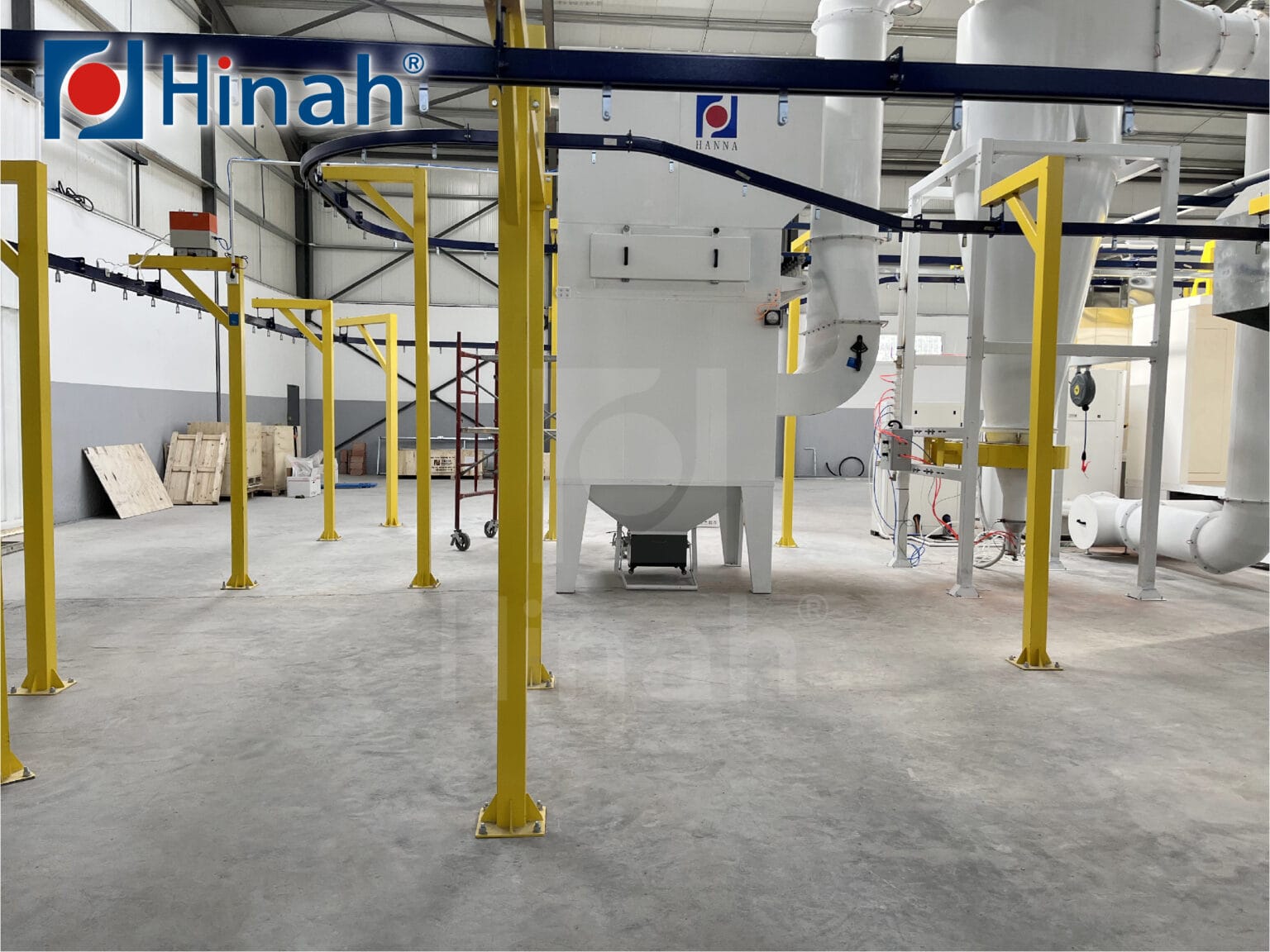
Root Causes of Chain Derailment in Powder Coating Line
- Sprocket Misalignment & Excessive Clearance
Misaligned drive sprockets are a leading culprit in chain derailments, often caused by worn shaft bearings or improper installation. When sprocket-to-axle clearance exceeds 0.15mm, angular deviations create uneven tooth engagement, forcing chains to “climb” and eventually jump tracks. In high-heat zones, thermal expansion exacerbates this issue—sprockets operating above 150°C require weekly alignment checks with dial indicators to maintain ≤0.5mm radial runout. Solutions include upgrading to tapered-lock sprocket bushings and implementing laser-guided alignment tools during maintenance to ensure perpendicularity within ±0.1° of the chain path.
- Inconsistent Chain Tension & Plate Distortion
Dual-strand systems demand tension parity—a 15% difference between chains causes one strand to slacken and “whip,” derailing at transfer points. Common triggers include deformed plates (>2mm curvature per 100mm length) or improper pre-tensioning during seasonal temperature shifts. For example, a 20°C ambient temperature drop increases chain tension by 12-18%, risking over-tensioned failures. Smart tensioners with load cells and IoT-enabled monitoring maintain optimal 20-30N/mm tension ranges, while quarterly plate straightness checks using optical comparators prevent distortion-related cascading failures.
- Contaminated Sprockets & Improper Installation
Chain derailments often trace back to overlooked debris—a 5mm³ metal fragment lodged in sprocket teeth can misdirect chains within 10 operational hours. Combined with worn sprockets (>3mm tooth tip rounding), contamination accelerates “tooth skipping” by 400%. Post-installation audits frequently reveal critical flaws: chains installed with >2° vertical misalignment relative to sprocket planes or guide rails exceeding 1.5mm/m straightness tolerance. Combat this through magnetic chip collectors in lubrication systems and mandatory post-maintenance checks using go/no-go sprocket gauges and 3D profilometers.
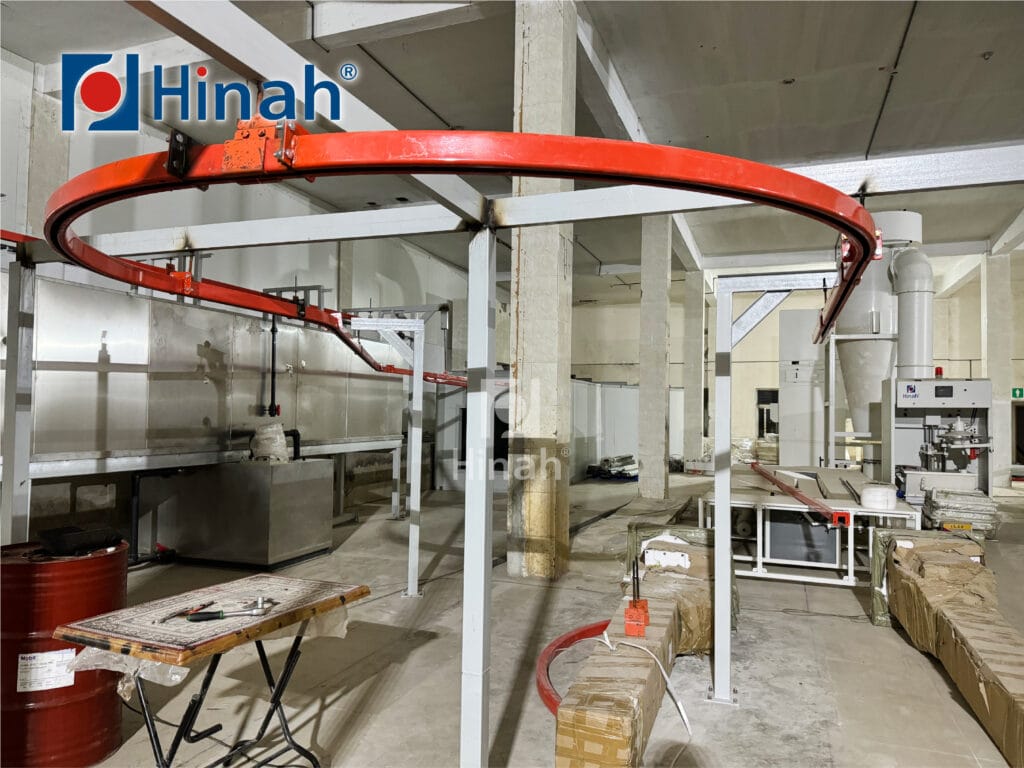

Critical Maintenance Oversights in Powder Coating Line Chains
- Neglected Base Plate Alignment
- Problem: >3mm/m base plate deviation causes 40% faster chain wear and derailment risks.
- Data: 70% of facilities skip annual laser-leveling checks.
- Fix: Install adjustable channel supports + quarterly digital inclinometer checks (±0.5° tolerance).
- Ignoring Seasonal Tension Adjustments
- Risk: 30°C temperature drop increases tension by 20%, risking chain fractures.
- Gap: 85% lines use static tension settings year-round.
- Solution: Auto-tensioners with thermal compensation (25-35N/mm adaptive range).
- Delaying Wear Threshold Repairs
- Red Flags: 3% chain elongation or >1mm plate wear depth.
- Cost: 80% breakdowns preventable with monthly checks (10-link length/3-point thickness tests).
- Action: Replace chains at 2.5% elongation preemptively.
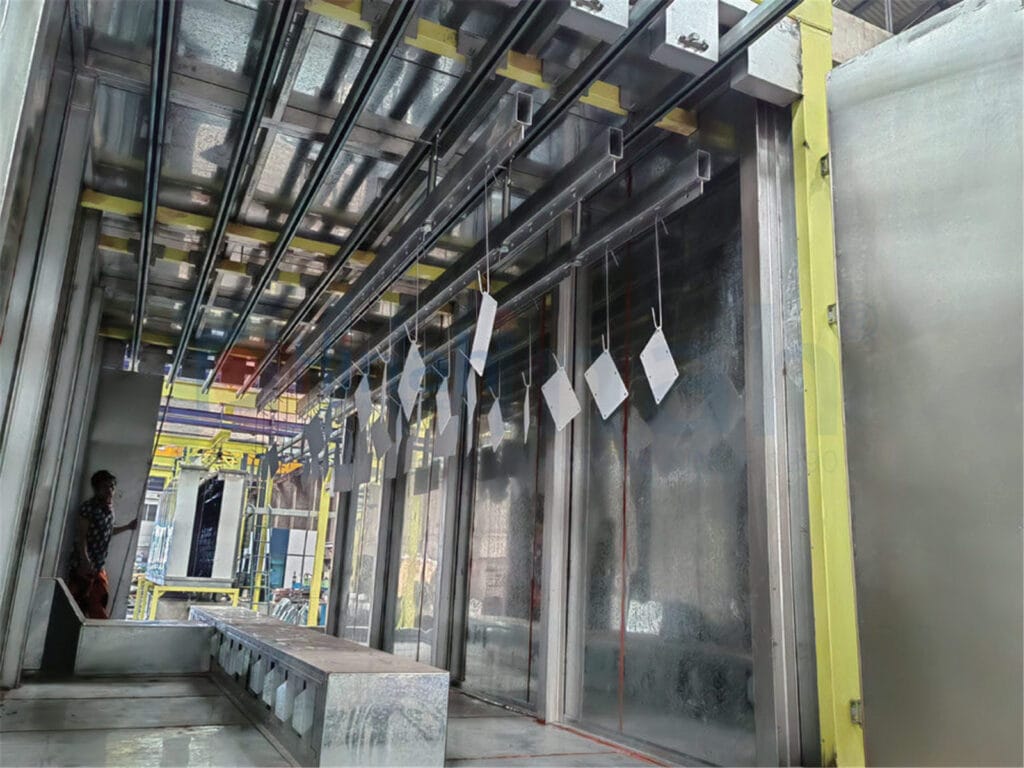
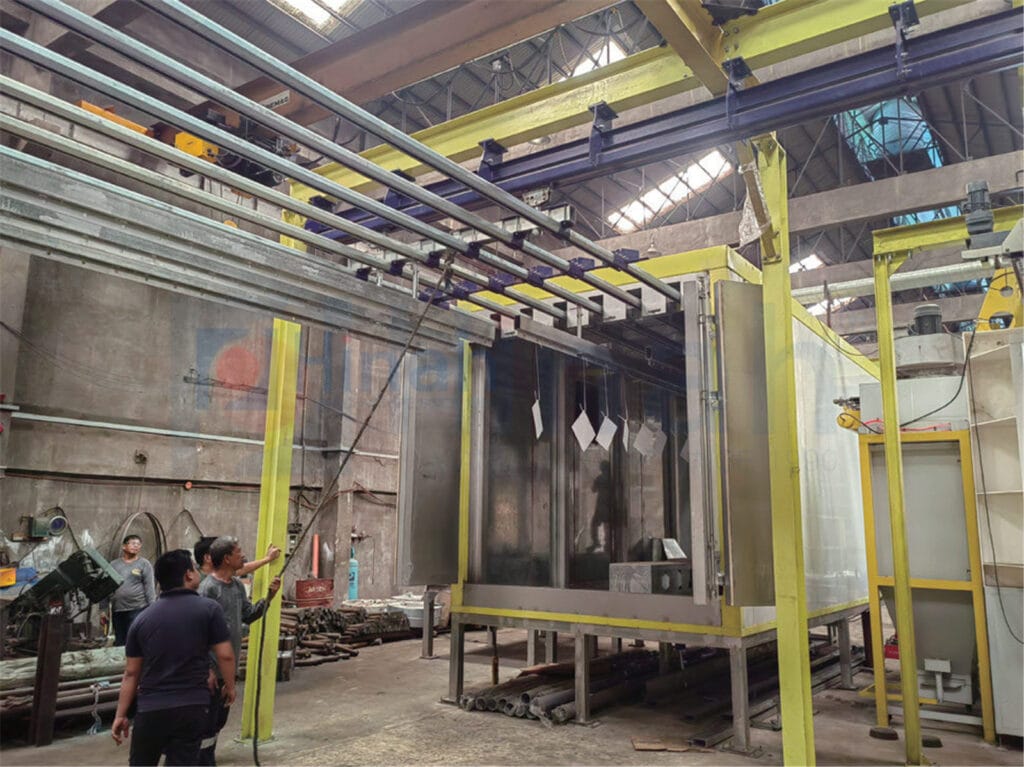
Conclusion
Conveyor chain failures in powder coating line are rarely sudden catastrophes—they’re the culmination of overlooked alignment issues, tension imbalances, and gradual wear. The key to preventing these disruptions lies not in reactive repairs, but in adopting a mindset of precision and prevention. By prioritizing regular alignment verification, dynamic tension adjustments, and early wear detection, manufacturers can transform their chain systems from vulnerability points into pillars of production stability.
Ultimately, every maintenance check and calibration effort is an investment in uninterrupted operations and consistent coating quality. Whether through advanced monitoring tools or disciplined inspection routines, the goal remains clear: catch minor deviations before they escalate. For facilities ready to break the cycle of breakdowns, the path forward starts with a simple step—partnering with experts to audit existing systems and implement tailored preventive strategies.