Powder coating has become a cornerstone of modern manufacturing, offering durability, aesthetic versatility, and environmental benefits. A critical factor in achieving high-quality finishes lies in selecting the right powder coating line for your operation. Two primary systems dominate the industry: manual powder coating lines and automated powder coating lines. Each has distinct advantages, limitations, and ideal use cases. In this article, we’ll explore these systems in detail, empowering you to make informed decisions for your production needs.
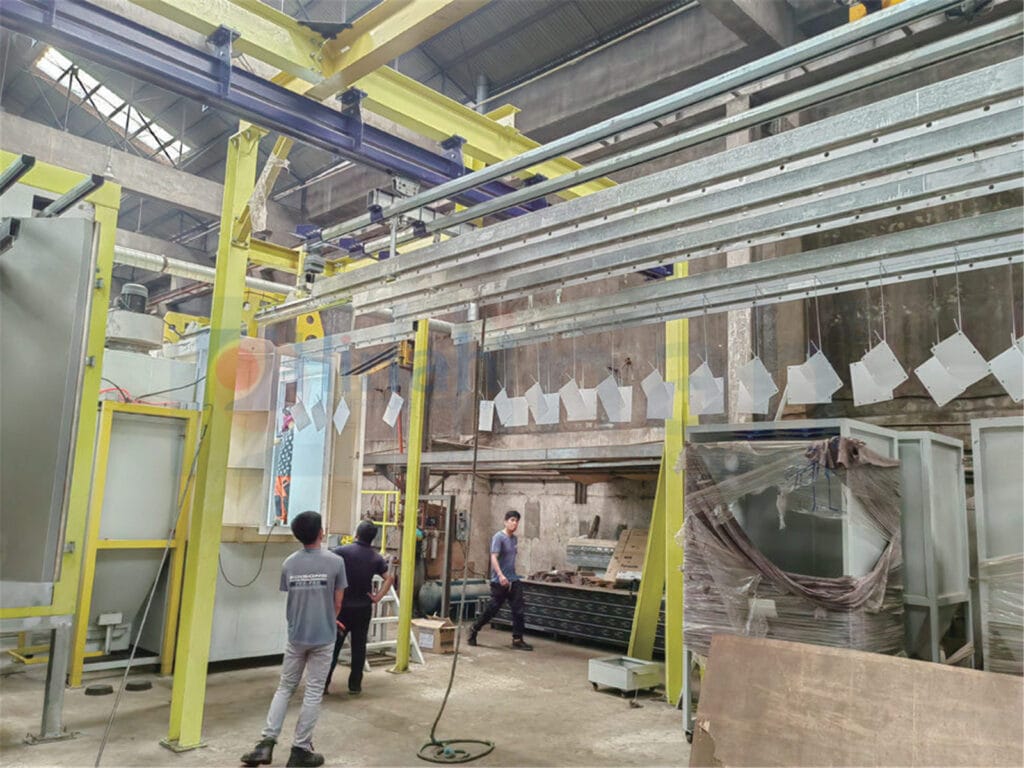
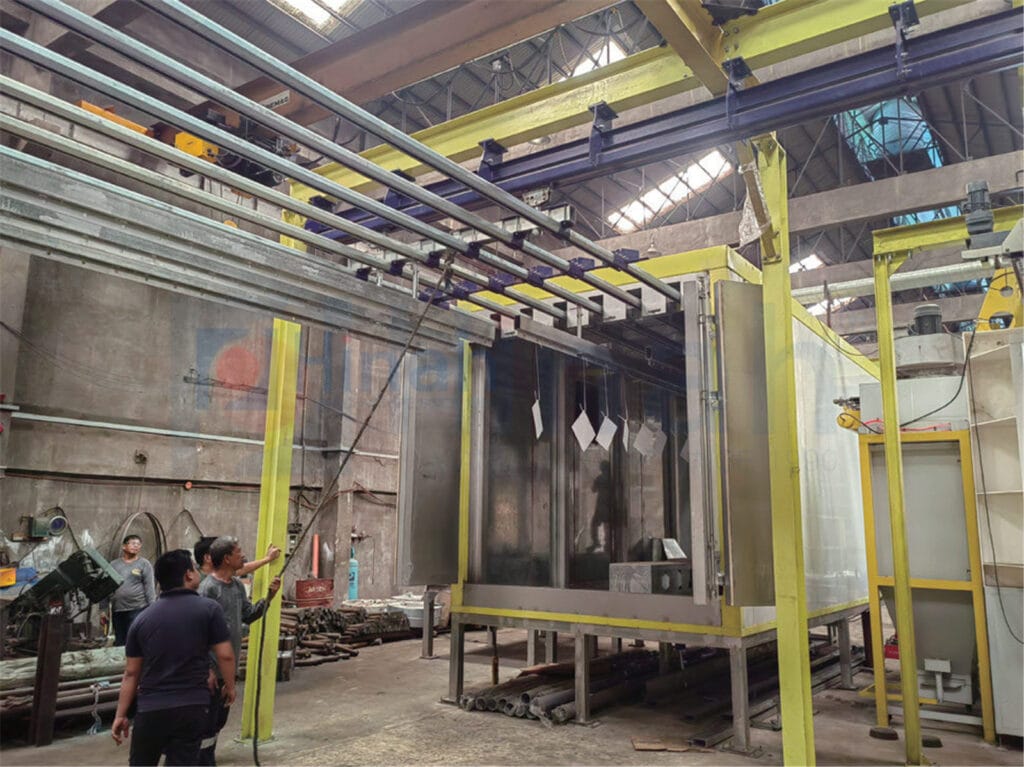
Manual Powder Coating Line
Manual powder coating lines rely on human operators to manage the entire coating process. From surface preparation to curing, workers handle tasks such as loading/unloading parts, applying powder, and monitoring quality.
Key Features of Manual Systems
Operator-Driven Process: Employees manually prepare surfaces (e.g., cleaning, sandblasting), load parts onto racks, and transport them through pretreatment, coating, and curing stages.
Flexible Workflow: Operators can adjust spray techniques, powder types, or curing times for custom jobs.
Simplified Equipment: Basic setups include a spray booth, curing oven, and manual conveyor or trolley system.
Advantages
Lower Initial Investment: Manual lines require less capital, making them ideal for startups or small businesses.
Adaptability: Suitable for low-volume production, custom projects, or prototyping, where frequent changes are needed.
Ease of Operation: Minimal training is required compared to automated systems.
Limitations
Labor-Intensive: Productivity depends on operator skill and speed, limiting throughput.
Inconsistency: Human error can lead to uneven coating thickness or missed spots.
Scalability Issues: Manual processes struggle to meet high-volume demands efficiently.
Ideal Applications
Manual systems shine in scenarios like:
Custom metal fabrication shops.
Repair and refinishing services.
Small-batch production of niche products.
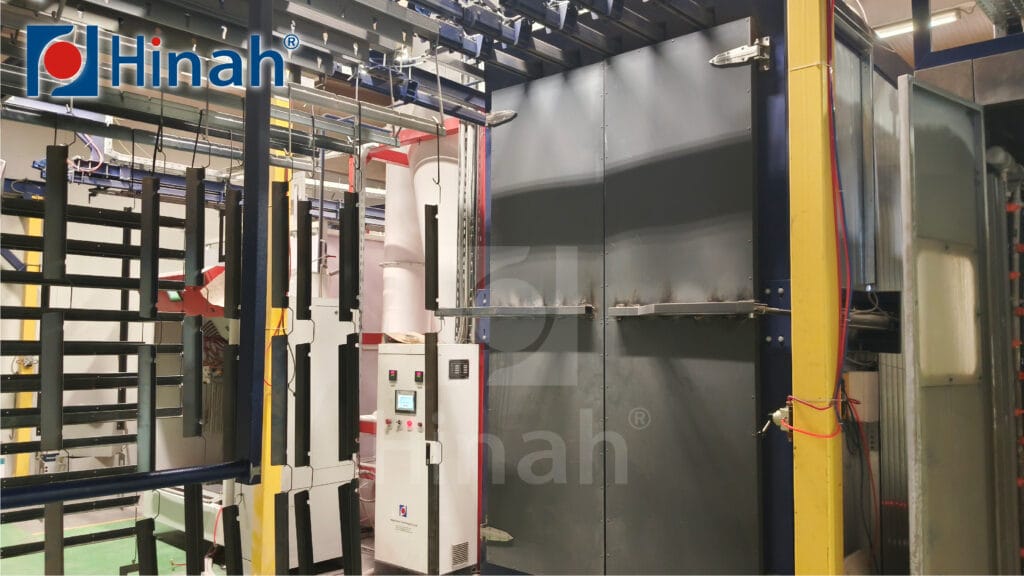
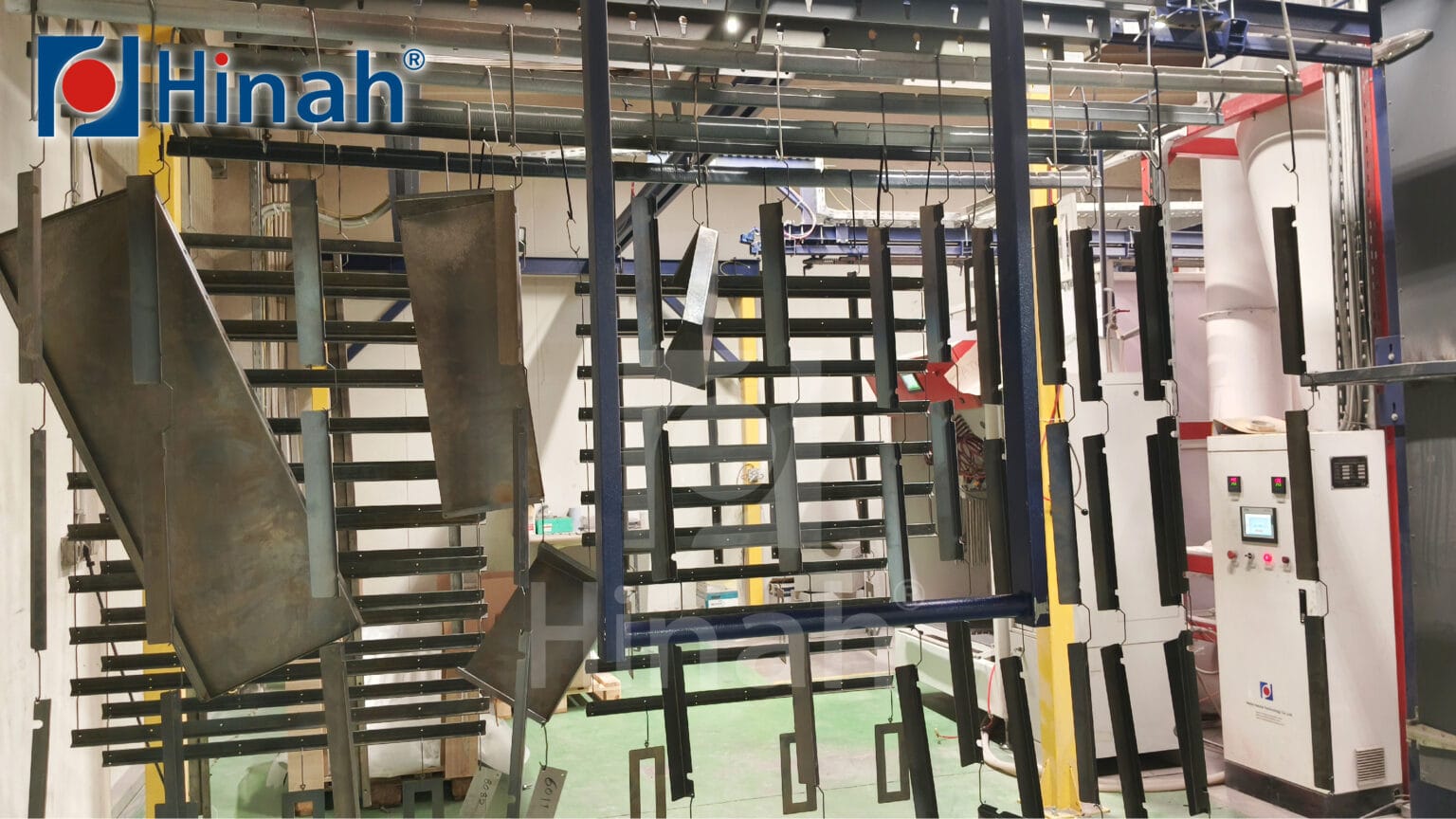
Automated Powder Coating Line
Automated powder coating lines integrate advanced machinery and software to streamline the coating process. These systems minimize human intervention, enhancing speed, precision, and repeatability.
Key Features of Automated Systems
Integrated Automation: Robotic arms apply powder with precision, while conveyor systems transport parts through pretreatment, coating, and curing stages.
Smart Controls: Programmable logic controllers (PLCs) monitor parameters like temperature, spray pressure, and curing time.
Closed-Loop Recovery: Excess powder is automatically collected, filtered, and reused, reducing waste.
Advantages
High Efficiency: Automated lines process large volumes quickly, with cycle times optimized for maximum output.
Consistent Quality: Robotics ensure uniform coating thickness and coverage, even on complex geometries.
Labor Savings: Reduced reliance on manual labor lowers long-term operational costs.
Scalability: Systems can be expanded or reconfigured to accommodate growing production needs.
Limitations
Higher Upfront Costs: Automation requires significant investment in equipment, software, and installation.
Complex Maintenance: Technical expertise is needed to troubleshoot robotic components or software glitches.
Rigidity: Retooling for new part designs or coatings may require downtime and reprogramming.
Ideal Applications
Automated systems excel in:
High-volume manufacturing (e.g., automotive, appliances).
Industries requiring strict compliance with quality standards.
Facilities prioritizing energy efficiency and waste reduction.
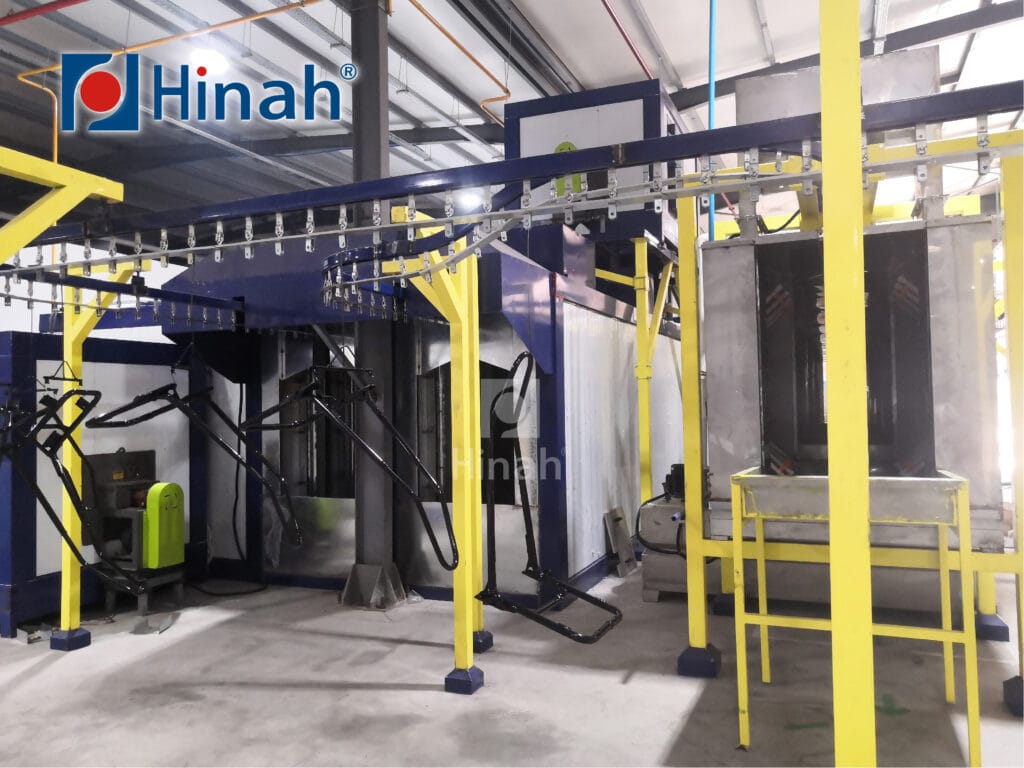
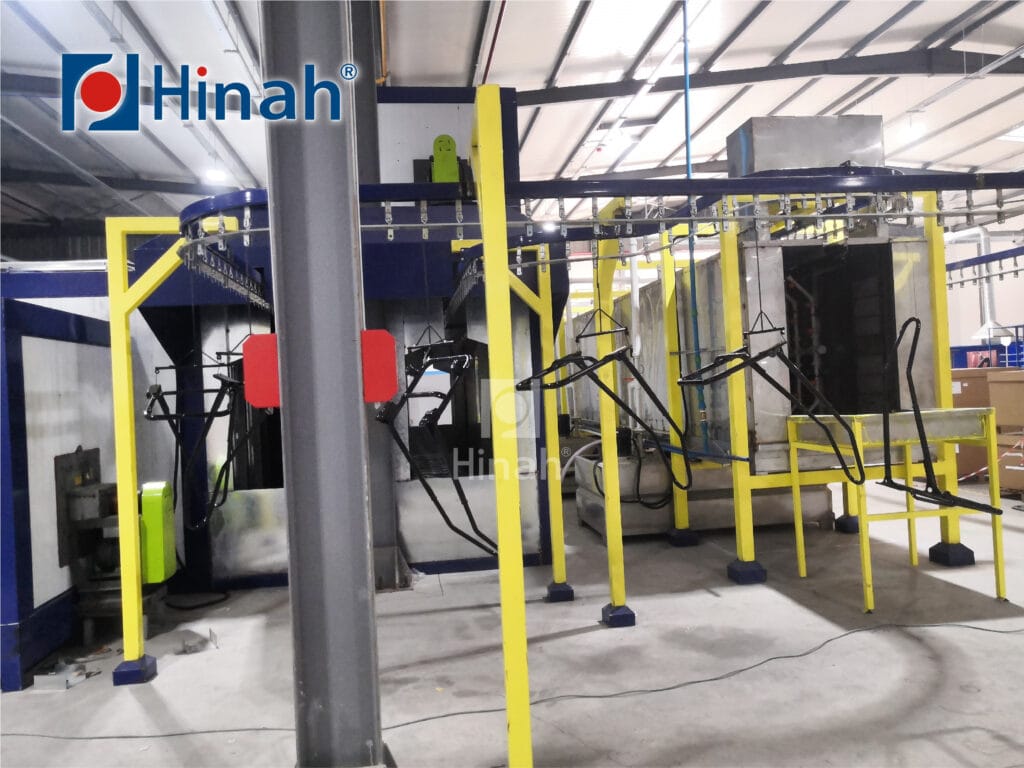
Manual vs. Automated: How to Choose the Right System
Choosing between manual and automated powder coating line hinges on evaluating your production needs, budget constraints, and long-term goals. For low-volume operations manual systems offer a cost-effective solution. Their affordability stems from minimal upfront investment in equipment and simplicity in operation, making them ideal for startups, custom fabricators, or businesses handling irregular or highly specialized orders. Manual lines also provide flexibility, allowing operators to adjust techniques for intricate designs or experimental coatings. However, reliance on skilled labor can lead to higher long-term operational costs and inconsistencies in output, particularly as production scales.
In contrast, automated powder coating lines are tailored for high-volume manufacturing, where speed, precision, and repeatability are non-negotiable. While the initial capital outlay for robotics, conveyor systems, and smart controls is substantial, automation slashes labor costs, reduces material waste, and ensures uniform quality across large batches. These systems excel in industries like automotive or appliance manufacturing, where standardized processes and strict compliance with quality standards are critical. However, their rigidity can pose challenges: Retooling for new part geometries or coatings may require downtime and reprogramming. For growing businesses, automated systems offer scalability through modular designs, allowing seamless capacity upgrades as demand increases. Ultimately, the decision balances immediate financial realities with future growth ambitions. Hybrid models, blending manual oversight with select automated components, are also gaining traction for manufacturers seeking a middle ground between adaptability and efficiency.
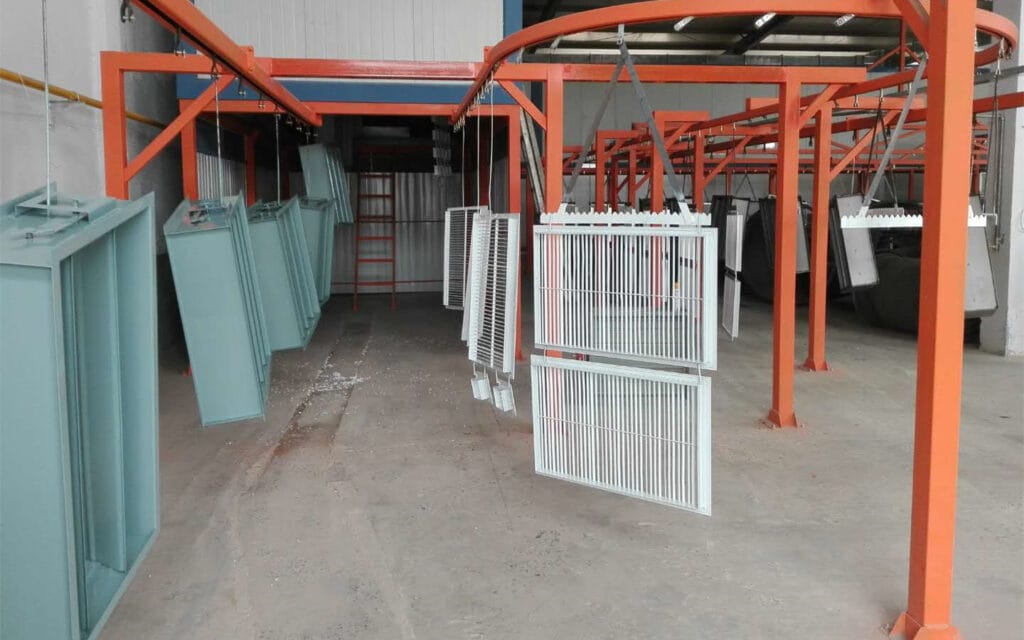
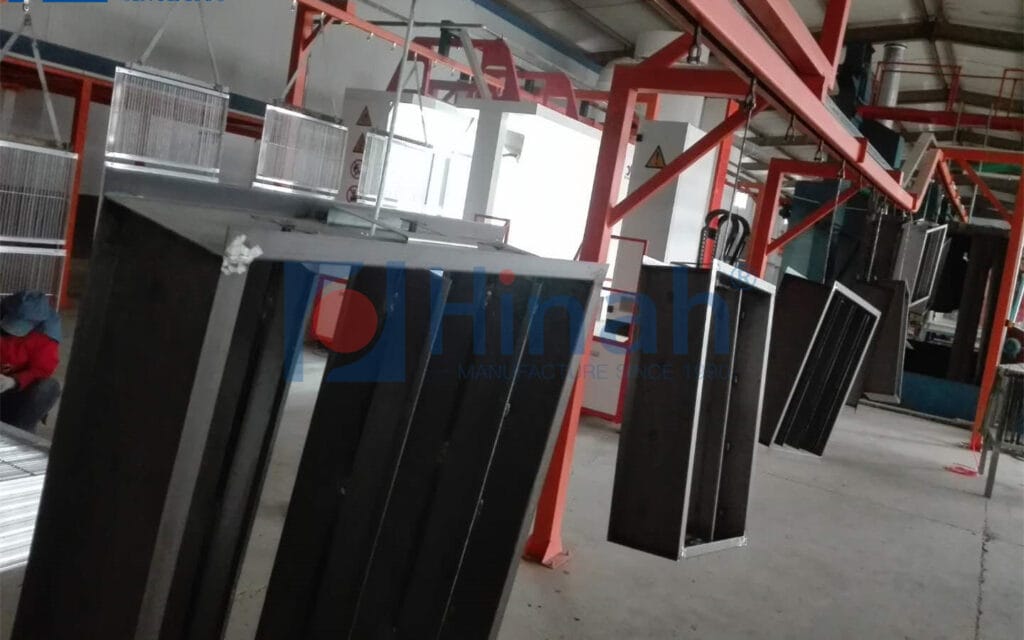
Conclusion
Both manual and automated powder coating line have distinct roles in modern manufacturing. Manual systems provide affordability and flexibility for small-scale or specialized projects, while automated solutions deliver unmatched speed and consistency for mass production. By evaluating your production needs, budget, and long-term goals, you can invest in a system that maximizes ROI and product quality.
As Industry 4.0 continues to revolutionize manufacturing, expect smarter automation—think AI-driven quality checks or IoT-enabled predictive maintenance—to further enhance powder coating efficiency. Stay ahead by aligning your coating line with tomorrow’s innovations today.