A powder coating line isn’t just a series of machines—it’s the heartbeat of your finishing process. Imagine a perfectly choreographed dance: parts glide smoothly from pretreatment to curing, operators work safely without bottlenecks, and every ounce of powder is used efficiently. That’s the power of a smart powder coating line layout.
A poorly planned layout, however, can lead to chaos. Think wasted time from backtracking parts, uneven coatings due to cramped spray zones, or even safety risks from overcrowded workstations. Optimizing your layout isn’t about fancy upgrades—it’s about aligning your space, workflow, and equipment to eliminate hidden costs and boost quality.
Whether you’re designing a new line or revamping an existing one, the right powder coating line layout ensures your operation runs like a well-oiled machine. Let’s dive into how you can transform your setup—no jargon, just actionable insights.
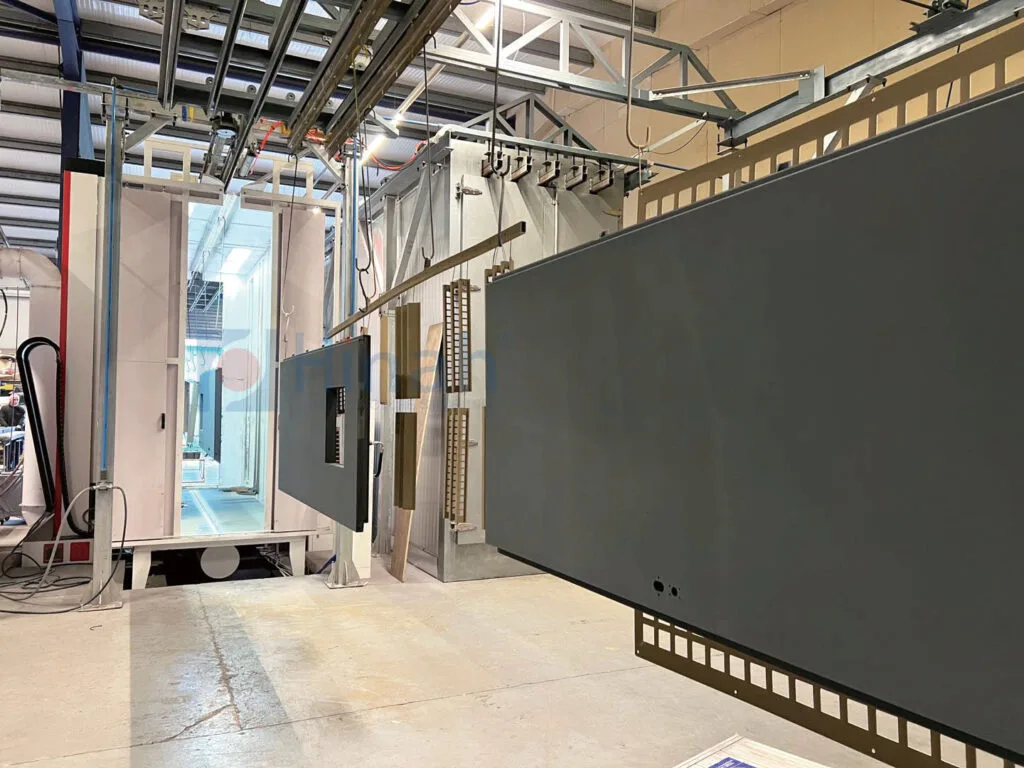
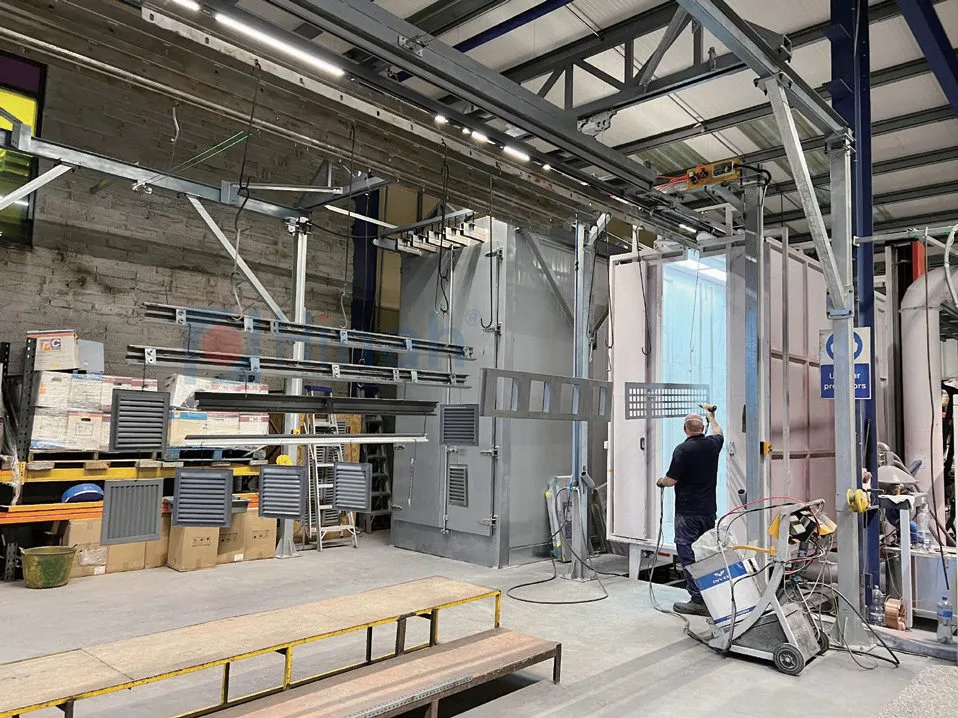
Key Factors to Assess in Your Current Powder Coating Line Layout
Space Utilization: Is Your Floorplan Working or Wasting?
Picture your shop floor as a puzzle—every machine and workstation needs to fit just right. If operators are squeezing past carts or the curing oven feels like it’s hogging prime real estate, your layout might be leaking efficiency. Maybe the powder coating booth is too close to the loading area, creating a traffic jam during shift changes. Or perhaps there’s a “dead zone” in the corner where tools pile up unused. Grab a floorplan sketch (even a rough one!) and ask: Does this space actually work for people, or are they constantly adapting to its quirks?
Material Flow: Are Parts Taking the Scenic Route?
Think about how parts travel through your powder coating line layout. Do they glide straight from pretreatment to curing, or do they detour like tourists lost in a maze? A conveyor that pauses too long before the oven isn’t just annoying—it’s a bottleneck waiting to happen. Maybe parts backtrack because the curing station is awkwardly placed, or they linger in transfer zones longer than a commuter stuck in rush hour. Watch the flow for a day: If you spot parts taking unnecessary U-turns, it’s time to rethink the roadmap.
Equipment Compatibility: Do Your Machines Play Nice Together?
Even the best equipment can underperform if it’s mismatched. Imagine a powder coating booth that’s wider than your conveyor’s reach—it’s like trying to park a truck in a compact spot. Powder recovery systems tucked too far from spray zones force operators to play fetch with wasted material. And if your robotic arm’s range doesn’t sync with the oven’s entrance? You’re leaving consistency (and profit) on the table. It’s not about having the shiniest tools; it’s about making sure they’re teammates, not rivals.
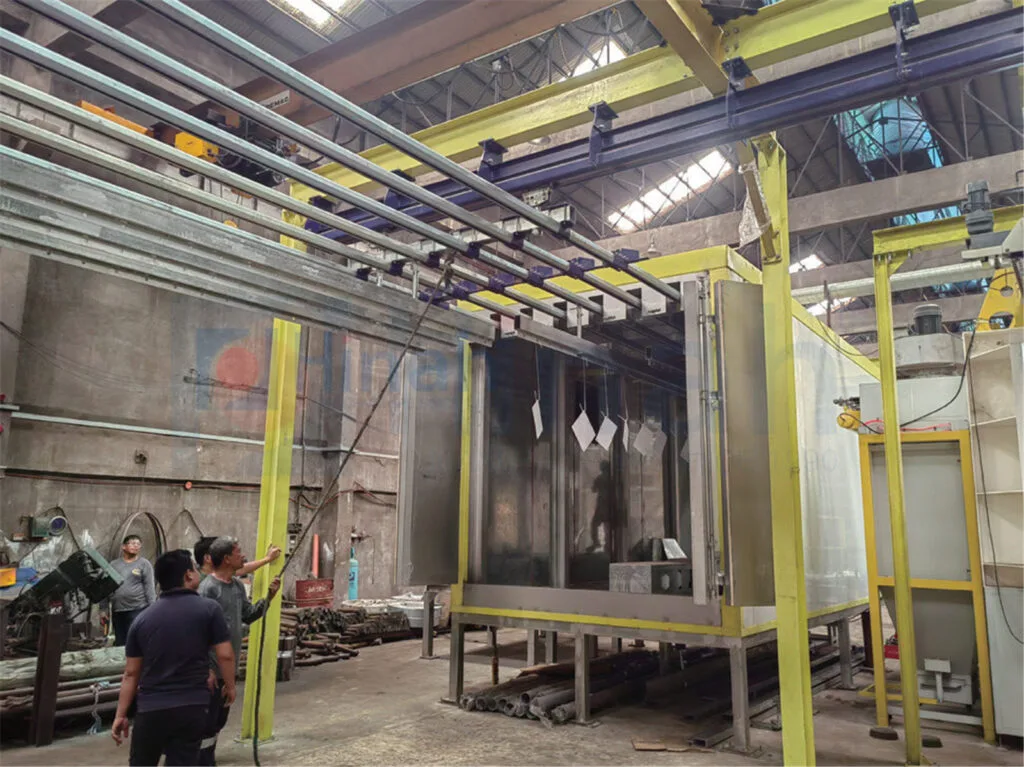
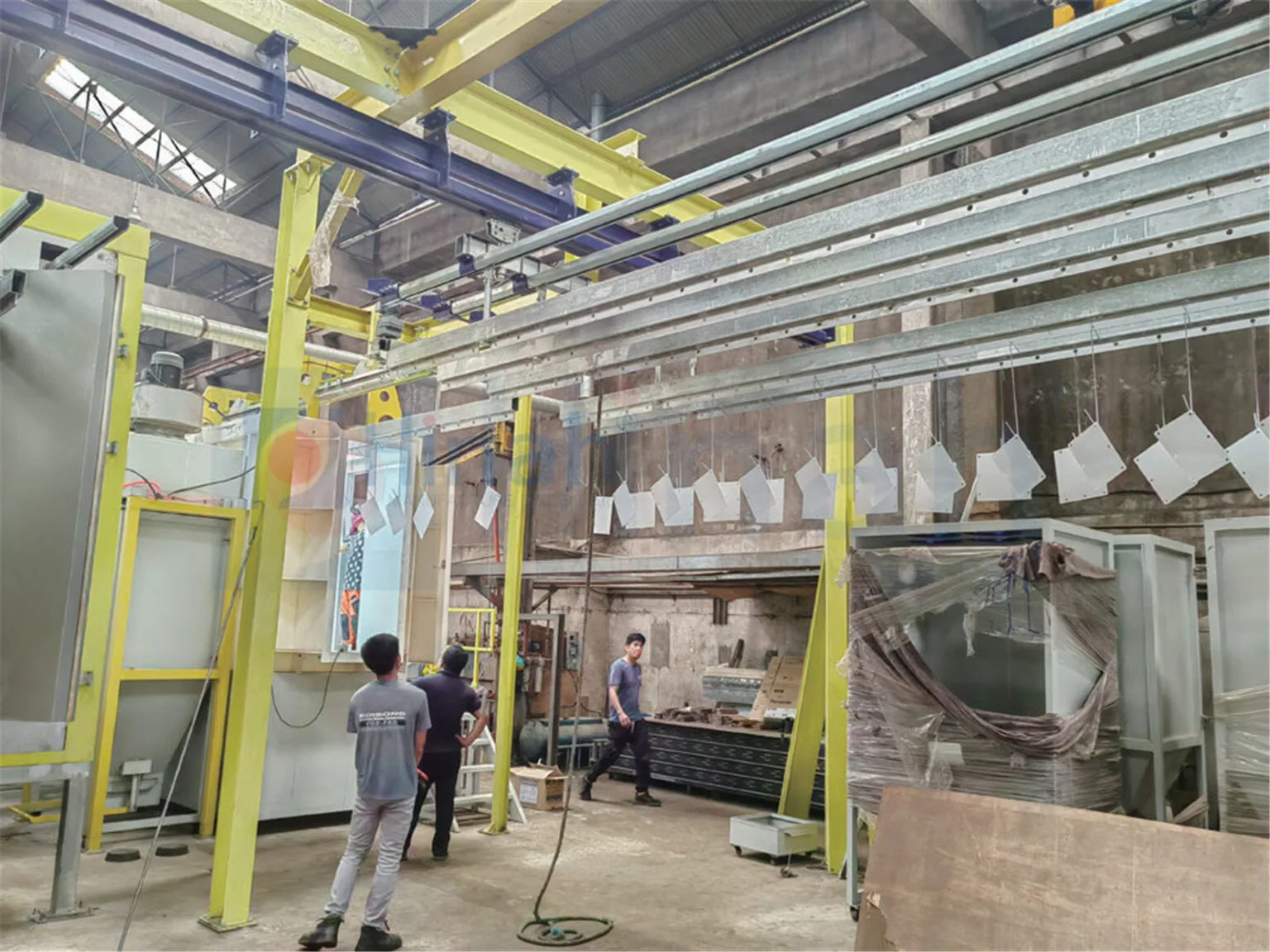
Step-by-Step Guide to Optimizing Your Powder Coating Line Layout
Space Planning Strategies
Think of your floorplan as a live chessboard—every move matters. Start by measuring the distance between workstations. Operators need enough room to maneuver without playing a game of “human Tetris.” Place the curing oven downstream from the spray booth to avoid heat creeping into your coating zone (trust us, melted powder isn’t a trend). Recovery systems? Keep them close to spray areas—like a loyal sidekick—to capture stray powder before it becomes expensive confetti. And don’t forget vertical space! Overhead conveyors or mezzanines can free up floor real estate for critical tasks.
Workflow Optimization
Your parts should glide through the line like a well-rehearsed ballet, not a bumper car rally. For high-volume shops, a straight-line layout minimizes backtracking and keeps the rhythm steady. Smaller operations might prefer a U-shaped design, where operators can pivot between stations like a chef in a compact kitchen. Match your conveyor speed to the oven’s appetite—if parts enter too fast, they’ll undercure; too slow, and you’re burning time. Pro tip: Time a few batches with a stopwatch. If the curing stage feels like a traffic light stuck on red, adjust the tempo.
Integrating Automation
Automation isn’t about replacing humans—it’s about giving them superhero tools. Robotic arms with electrostatic sprayers can nail consistent coatings, even on tricky geometries (goodbye, “thin spots”). Add smart sensors to monitor airflow and humidity, tweaking settings in real time like a self-adjusting thermostat. And if you’re nervous about upfront costs, start small: Automate just the recovery system or one spray booth. Think of it as training wheels for your powder coating line layout—soon enough, you’ll wonder how you ever worked without it.
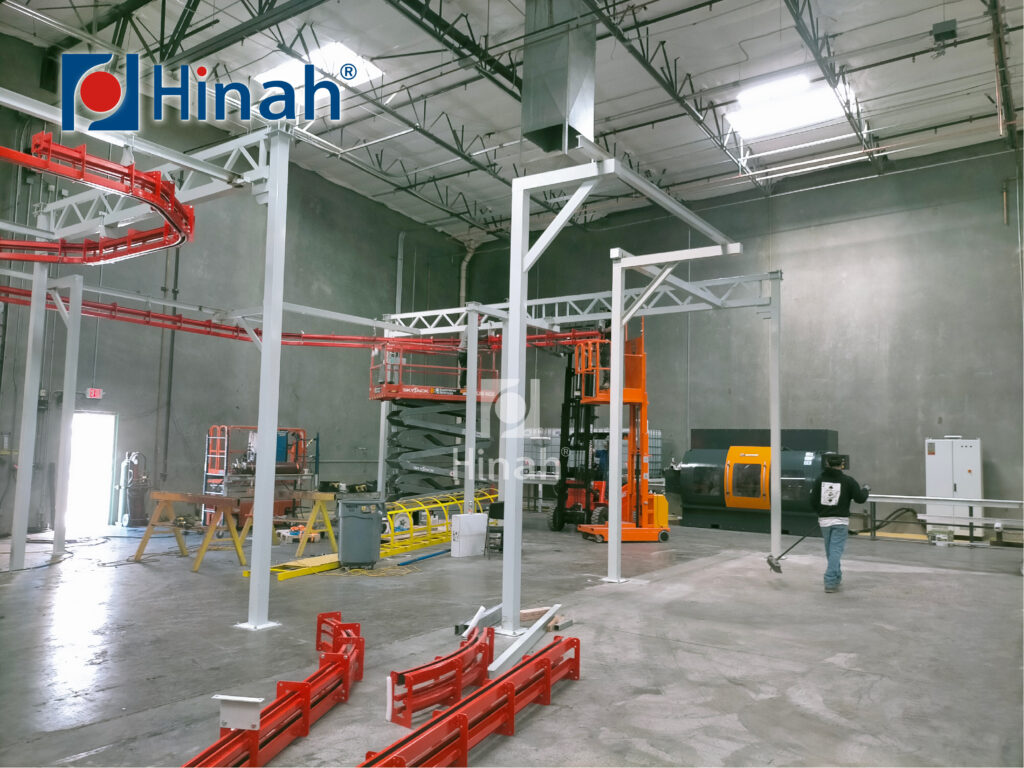
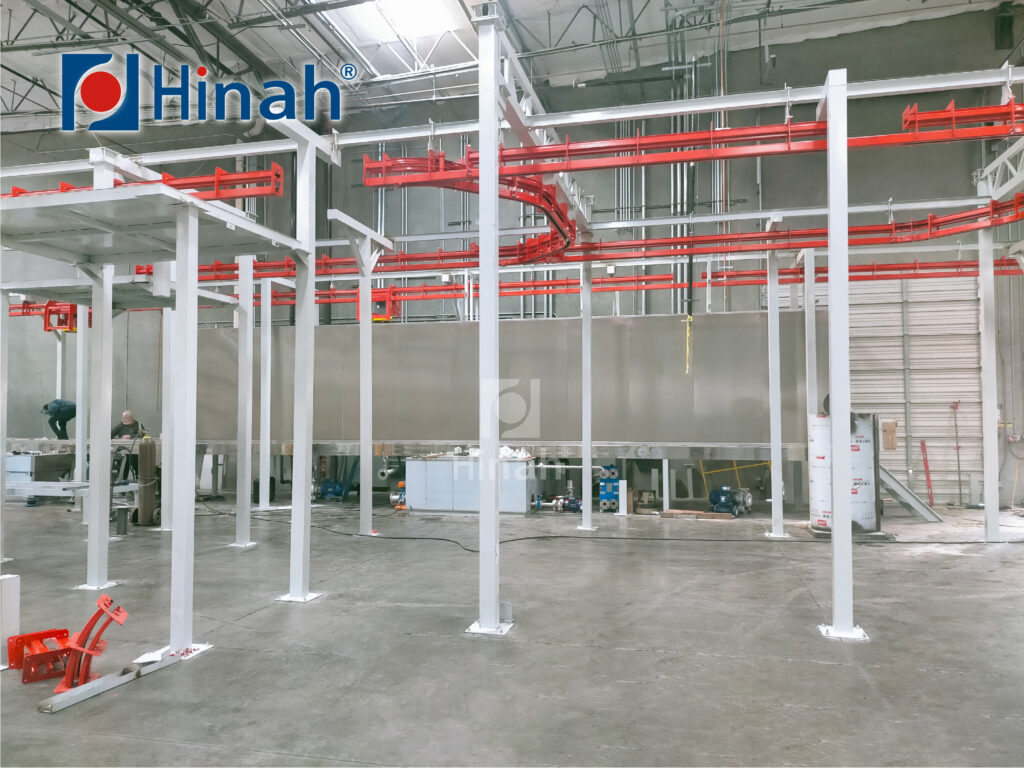
Common Mistakes to Avoid in Powder Coating Line Layout Design
- Overcrowded Work Zones
A poorly optimized powder coating line layout often sacrifices spacing for short-term space savings. Tight gaps between pretreatment, spraying, and curing stations increase contamination risks (e.g., oil mist settling on coated surfaces) and hinder operator efficiency. For consistent quality, ensure at least 3–5 feet of clearance between critical zones.
- Inadequate Ventilation Systems
Poor airflow design leads to excessive powder overspray accumulation, raising fire risks and cleanup costs. Ensure spray booths have dedicated exhaust systems with appropriate CFM (cubic feet per minute) ratings, and position intake vents to avoid recirculating contaminated air.
- Static Workflow Design
Rigid layouts that lack scalability force costly redesigns when production demands change. For example, lines built exclusively for small parts may struggle to accommodate larger components. Incorporate modular zones or leave expansion space for future upgrades.
- Misaligned Process Sequencing
Placing curing ovens upstream of spray booths or creating indirect part pathways introduces delays and energy waste. Optimize workflow continuity by arranging stations in a logical sequence (pretreatment → coating → curing → inspection).
- Neglecting Maintenance Access
A powder coating line layout that blocks equipment access invites downtime. Ensure technicians can safely service conveyors, recovery systems, and ovens by allocating at least 2 feet of clearance around all machinery.
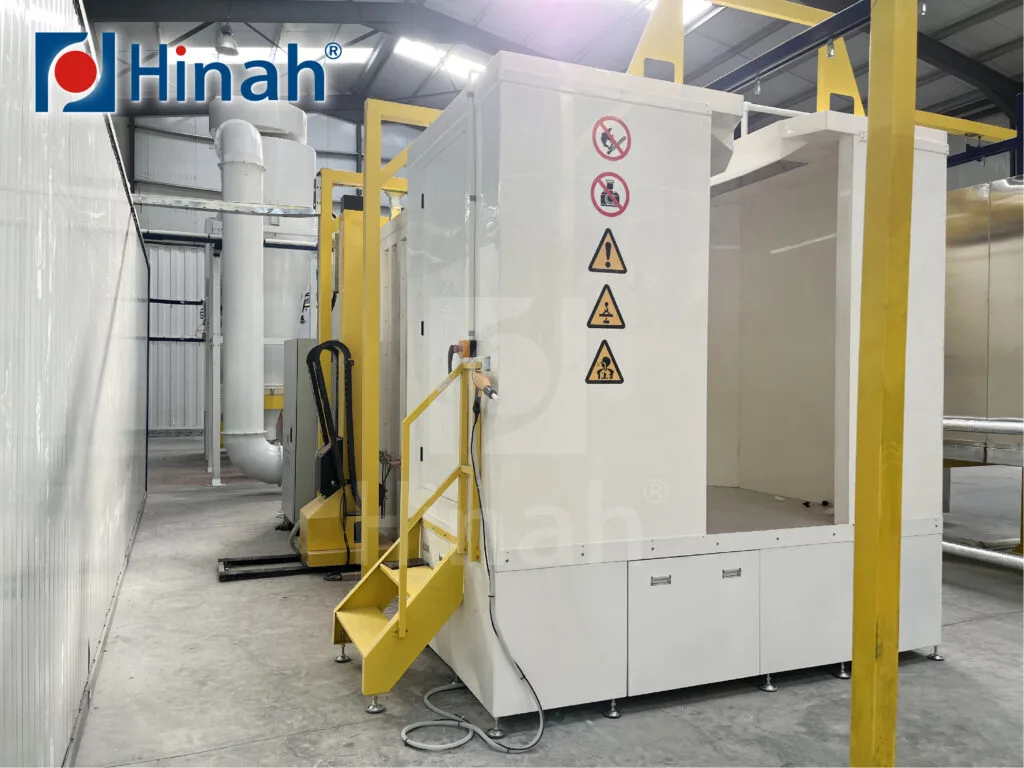
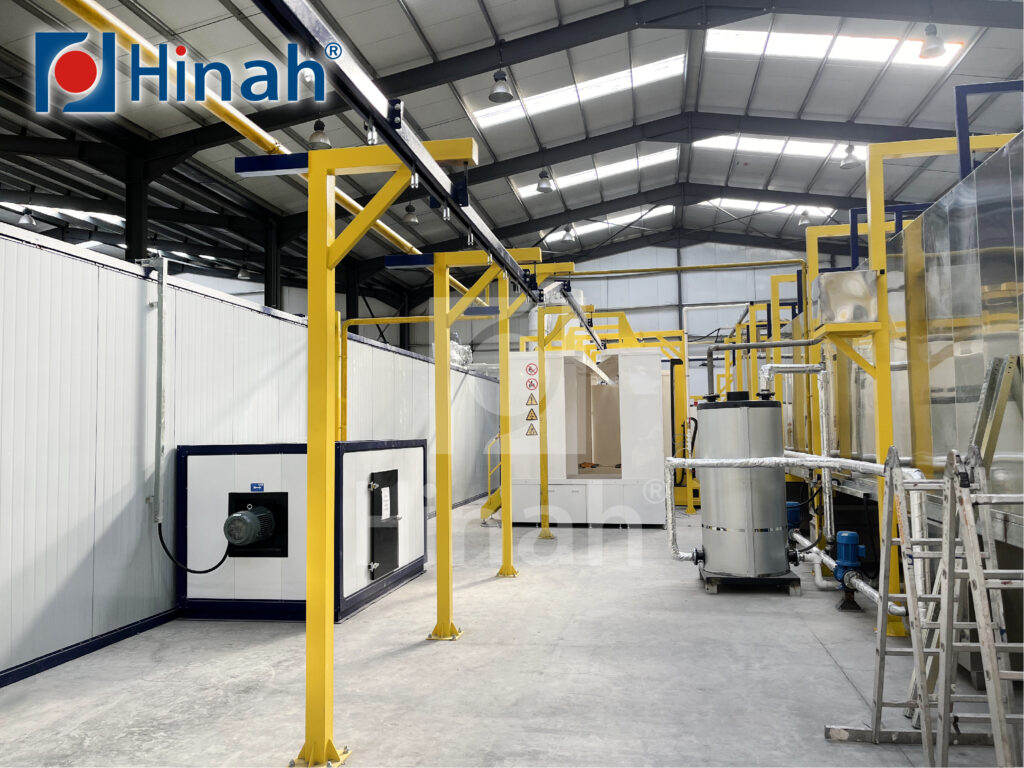
Conclusion
Optimizing your powder coating line isn’t a one-time task—it’s an investment in efficiency, quality, and scalability. By addressing space utilization, workflow sequencing, and automation integration, you can eliminate bottlenecks, reduce material waste, and future-proof your operation.
Avoid common pitfalls like overcrowded zones or static designs that limit adaptability. Instead, prioritize logical station sequencing, maintenance-friendly spacing, and modular flexibility. Whether you’re retrofitting an existing line or designing a new one, small adjustments to your powder coating line layout can yield outsized returns—from faster cycle times to higher customer satisfaction.
Ready to take the next step? Contact our experts for a customized layout audit or explore our powder coating equipment solutions to elevate your line’s performance.